このガイドでは、レーザー支援加工の技術と、従来の加工にレーザーを組み込むことでどのように能力が向上するかについて説明します。レーザーと材料間の相互作用の原理と、加工パラメータの最適化方法について説明します。また、各業界における実際のアプリケーションと、精密レーザー製造の将来的な展望についても考察しています。
レーザー支援金属加工:精密切断と表面処理
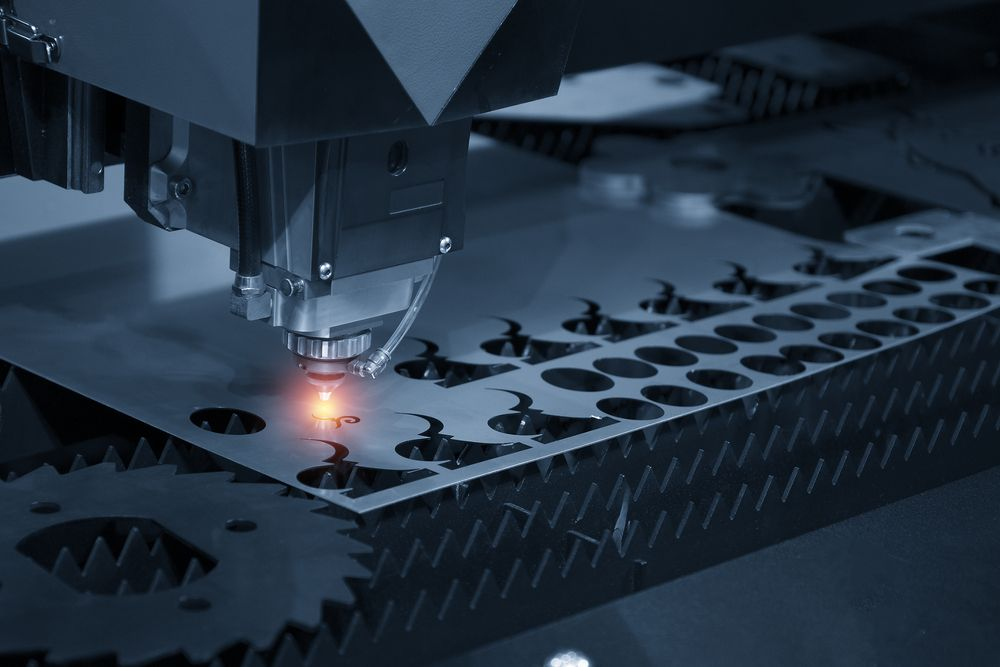
レーザーベースのハイブリッド加工プロセスは、ここ数十年で精密製造に革命をもたらしました。従来のサブトラクティブ工具に高出力レーザー光源を組み込むことで、これらの技術は、従来の方法だけでは限界を超えていた材料加工の新たな可能性を解き放ちます。
レーザーの特性と設定によって支配されるレーザーと物質の相互作用により、これらのプロセスは、効率的な材料の除去、修正、および構造化に向けて、熱的、物理的、および化学的効果を設計します。加工材料の特性に合わせてレーザーパラメータを慎重に制御することで、加工結果を最適化します。
この柔軟性により、レーザー支援加工は、これまで機械的手段のみでは切断が困難とされていた、問題のある金属、合金、セラミック、複合材に取り組むことができます。このようなハイブリッドシステムは、基本的な切断や穴あけだけでなく、硬化表面から微細パターン形状に至るまで、革新的な機能を実現します。
業界を問わず、レーザーハイブリダイゼーションは高精度製品の工程効率、品質、精度を大幅に向上させます。この技術の強化に関してはまだ多くの研究が行われていますが、製造アプリケーションの利便性は、自動車製造を中心に、ほとんどの産業ですでに広く受け入れられています、 航空宇宙 そして 医療産業.この記事は、比較的新しいレーザー支援加工分野の一般的な紹介を目的としています。主な原理を要約し、プロセスの最適化に関する研究をレビューし、この急成長中の技術を使用したアプリケーションを紹介します。また、精密レーザー製造の将来の展望についても考察しています。
レーザー加工パラメータ
レーザー加工プロセスに影響を与える主なレーザーパラメータは、レーザー出力、波長、パルス周波数などです。レーザー出力は、加工物に供給されるエネルギー量を決定します。出力が高いほど材料除去が速くなりますが、熱影響ゾーンが発生する可能性があります。波長もまた 加工 - 短い波長は表面でよく吸収され、長い波長は深く浸透します。
パルスレーザではパルス周波数が重要です。高い周波数は、より高速な除去のために高いピーク出力を可能にしますが、低い周波数は熱影響部を最小化するのに役立ちます。これらのパラメータの適切な最適化は、材料と望ましい結果に基づいて必要です。
素材に関する考察
熱伝導率、硬度、加工硬化挙動などの材料特性も、レーザー加工に大きな影響を与えます。熱伝導率の高い材料は、熱の放散が速く、熱応力を低減します。しかし、加工は難しくなります。硬い材料は、除去に高いエネルギー密度が必要です。
鋼鉄のように加工硬化が強い材料は、加熱すると表面が硬化するため、さらに高いエネルギー密度が要求されます。レーザーパラメータと材料特性の間のこれらの相互作用を理解することは、各アプリケーションで最適な結果を得るためのプロセスのカスタマイズに役立ちます。良好な表面仕上げと寸法精度で効率的な加工を行うためには、加工物の材料に基づいて加工パラメータを調整する必要があります。
レーザーアシスト加工の利点
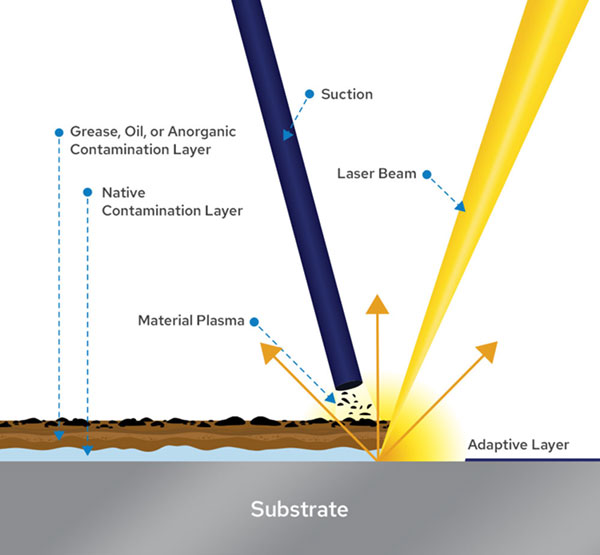
レーザーアシスト加工は、従来の非レーザーアシスト加工プロセスよりもいくつかの利点があります。主な利点として、切削抵抗の低減、表面粗さの低減、工具摩耗の低減、材料の微細構造と特性の変化が挙げられます。
レーザーによる局所的な熱処理は、工具前方の被削材を軟化・軟化させることにより、工具にかかる切削力を大幅に低減します。これにより、工具への機械的および熱的負荷が軽減されます。また、軟化した被削材は、従来の加工と比較して表面粗さが減少し、優れた仕上げ面が得られます。
工具負荷と温度が低いため、工具摩耗が少なく、工具寿命が延びます。実験によると、非レーザー加工と比較して工具寿命が最大10倍と大幅に向上しています。レーザー熱サイクルはまた、非常に局所的なレベルで材料の微細構造と硬度を変更します。これにより、表面の硬化などの応用が可能になります。
全体として、レーザーの導入は、より良い表面品質とともに、より高い材料除去率を可能にすることで生産性を向上させます。摩耗の減少による工具コストの削減と相まって、レーザーアシスト加工は、特に難削材において、従来の方法よりも部品の経済性を向上させます。
特定材料のレーザー加工に関する研究
ニッケル合金
ニッケル合金は、その高い強度と耐食性により、航空宇宙産業や医療産業で広く使用されています。しかし、微細構造が緻密なため、加工が困難です。150~300Wの出力と2~4mm/分の送り速度のNd:YAGレーザーが、インコネル718の切断品質を最適化することが研究で示されています。レーザー支援旋盤加工は、従来の旋盤加工と比較して、スラスト力を40%、切削温度を30℃低減し、表面粗さ0.4μmを達成します。
チタン合金
Ti6Al4Vのようなチタン合金は、その高い強度と耐食性により、航空機用タービンに一般的に使用されています。しかし、その化学反応性は加工に課題をもたらします。研究では、1070nmのファイバーレーザーを使用し、3kWの出力と500mm/minの送りでTi6Al4Vの加工を最適化しました。これにより、切削抵抗と比切削エネルギーが半減し、表面粗さが0.8μmとなり、レーザーを使用しない場合の2.5μmと比較しました。
セラミックス
窒化ケイ素とアルミナ・セラミックスは、高い硬度と強度を必要とする用途に使われています。しかし、脆いため、レーザー以外のプロセスではクラックが発生しやすくなります。レーザーは、クラックのないセラミックスを加工するために、より低いエネルギーでマイクロEDMのようなプロセスを可能にします。窒化ケイ素のNd:YAGレーザー加工を最適化したところ、200Wの出力と50mm/分の送りにより、クラックのない0.2μmの粗さの表面が得られました。
複合材料
EPRIによると、炭素繊維およびガラス繊維強化ポリマー複合材料は、高い剛性と重量に対する強度を有するため、引き続き広く使用されています。レーザーはポリマーマトリックスのみを除去し、その高い強度により完全なファイバーはきれいなエッジ仕上げを提供します。研究によると、CO2 レーザー切断 3kWの出力と300mm/minの送り速度で炭素繊維複合材料の切断を行うと、剥離のない1μm以下の粗さの切断面が得られます。
要約すると、材料特性に基づいてレーザーパラメータを最適化することで、切断が困難な合金、セラミック、および複合材料の効率的で損傷のない加工が可能になります。これにより、生産性が向上し、航空宇宙および医療用途の厳しい要求を満たすことができます。さらなる研究により、レーザー加工能力を他の材料に拡大することができます。
レーザー支援加工における高度な切削技術
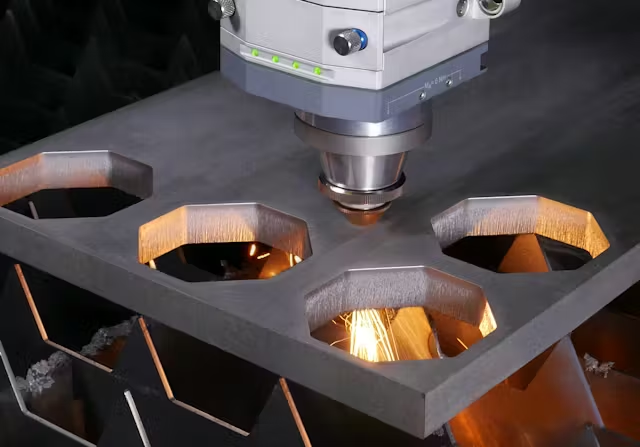
レーザーによる旋盤加工とフライス加工
以下は、頻繁に使用される金属除去プロセスの一部です; 旋回 とフライス加工。旋削加工では、ワークが回転する間に切削工具が回転し、切削加工によって両方の円筒面が作られます。フライス加工では、複数の歯を持つカッターが回転し、ワークピースの面を横切るように送りながら材料を削り取ります。
これらの加工にレーザーを組み込むことは、難しい材料の加工に役立ちます。旋削加工では、集光レーザーが工具の前にある材料を予熱し、切削力と温度を下げます。これにより、合金を加工する際の工具の応力が軽減され、寿命が延びます。フライス加工では、スキャンされたレーザーが次に除去する被削材を選択的に軟化させ、表面品質を向上させ、より高い材料除去率を可能にします。
チタンやニッケル超合金の旋削加工にレーザーを使用した場合、工具寿命が40-60%向上し、力が減少することが研究で実証されています。イッテルビウムファイバーレーザーを使用したインコネル718のフライス加工では、従来の方法と比較して3倍高い材料除去率を示しました。
パルスレーザーの切断への影響
連続発振レーザとは対照的に、パルスレーザは切断中の熱処理をより高度に制御します。パルスレーザの高いピーク出力は、迅速な局所加熱を可能にし、パルス間遅延は照射間の熱放散を助けます。
研究によると、レーザーパルスの持続時間と繰り返し速度を最適化することで、切削ゾーンの温度を臨界レベル以下に維持し、工具の損傷を防ぐことができます。パルス間遅延を大きくした短いパルスは、熱影響部を最小限に抑えます。パルスCO2レーザは、連続レーザと比較して、チタンのフライス加工における表面酸化を低減します。
パルスファイバーレーザーは、個々のミクロン単位のスポットで予熱および切断する能力により、硬鋼旋削における材料除去率を最大化します。この局所的な加熱により、パルスレーザは連続レーザに比べて工具や表面への熱影響を最小限に抑えることができます。
レーザー加工による表面テクスチャリング
レーザー表面硬化
レーザー表面硬化は、レーザービームの高エネルギー密度を利用して、母材の内部特性に影響を与えることなく、薄い表面層を迅速に熱処理します。これにより、耐摩耗性と耐腐食性のための硬いケースが外面に形成されます。
適切なレーザーパラメーターを使用したレーザー硬化は、処理表面の硬度、摩耗、および腐食性能を大幅に向上させるという研究結果があります。例えば、AISI 4340鋼を1.5kWの出力でNd:YAGレーザー処理すると、0.5mmの硬化層が形成され、母材と比較して硬度が50~60%増加します。
同様に、チタン合金のレーザー硬化は、表面硬度を30-40%高め、耐摩耗性を3倍にします。105K/sを超えるレーザー処理の急速な加熱および冷却速度は、硬化の原因となる非平衡相を促進します。また、サイクルを高速化することで、熱影響部を最小限に抑えることができます。
レーザー焼入れは、摩擦や摩耗を受ける歯車、金型、その他の部品に非常に効果的です。このプロセスは、工業部品の機能寿命を向上させ、メンテナンスの必要性を低減します。他の表面硬化技術に代わる、環境にやさしく汎用性の高い技術を提供します。
レーザー表面パターニング
レーザーを用いた精密な表面テクスチャリングは、表面特性の向上やカスタマイズを必要とする様々なアプリケーションを可能にします。レーザーで生成されたマイクロ/ナノ構造は、濡れ性、接着性、トライボロジー、光学的特性を変化させます。
フェムト秒レーザーによるサブミクロン形状の金属表面構造化は、酸化剤の拡散を阻害することで耐食性を向上させるという研究結果があります。セルフクリーニング 超撥水 蓮の葉を模倣した階層構造をレーザーで形成することで、チタンなどの金属に表面を形成。このような表面は、水接触角160°以上、すべり角10°未満を示します。
ガラス上の反射防止および防汚ナノグレーティングは、レーザー干渉リソグラフィーを用いてサブ波長リッジのアレイを形成します。バイオメディカルインプラントは、海綿骨構造に類似したレーザーマイクログルーブトポグラフィにより、オステオインテグレーションが促進されます。
レーザーは、制御されたフィーチャサイズで、大面積にわたる滑らかで均一なパターンを迅速に加工することができます。3Dナノパターニングは、勾配表面特性と多機能性を可能にします。非接触レーザープロセスにより、汚染の問題を回避できます。
全体として、レーザー表面工学は、微細構造と特性の調整を通じて、自動車、消費者製品、生物医学インプラントなどの産業にわたるインテリジェントな表面設計に新たな道を開きます。
結論
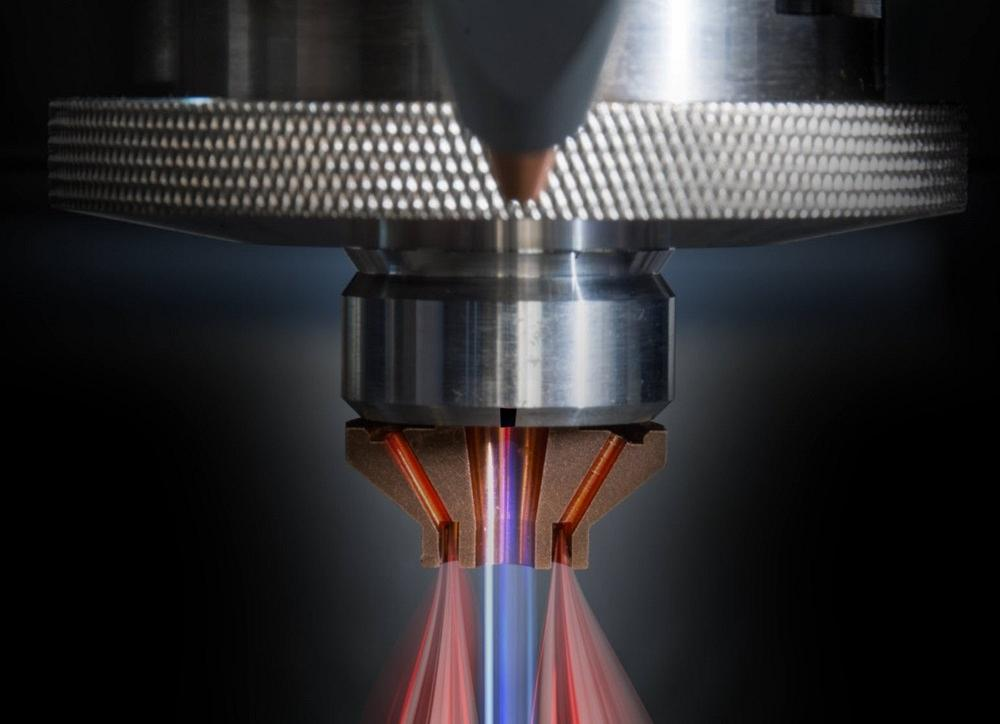
レーザー支援加工は、従来の方法に比べて大きな利点を提供する非常に効果的な製造技術として登場しました。レーザーの精密な加熱効果により、従来は加工が困難とされていた幅広い材料の加工能力を向上させることができます。
被加工材の特性に基づき、切断パラメータと共にレーザパラメータを最適化することで、プロセスの生産性、部品品質、および工具寿命を最大限に改善することができます。特にパルスレーザは、加工物の損傷と工具の磨耗を最小限に抑えるために、熱影響に対する優れた制御を提供します。
基本的な切断作業だけでなく、レーザーを統合することで、硬度処理やカスタマイズされた表面テクスチャのような新しい可能性が開けます。これにより、多くの産業にわたる機能化コンポーネントへの応用が拡大します。広範な研究が続けられている一方で、レーザー技術の工業的実装は、特に要求の厳しい高価値のアプリケーションにおいて、その技術的および経済的な利点をすでに実証しています。
さらなる進歩により、レーザー加工は従来のサブトラクティブ・プロセスをますます強化し、さらには取って代わります。その柔軟性と非接触の性質は、先進的な製造の道を発展させ続けるでしょう。全体として、レーザーベースのハイブリッド加工は、高精度の機能部品や設計された表面を効率的に製造する上で、将来への大きな可能性を示しています。
よくあるご質問
Q.レーザー加工機はどのように金属を加工するのですか?
A.高出力レーザーを金属加工物に照射し、レーザーエネルギーで材料を溶融、蒸発、除去します。正確な位置決めシステムにより、様々な形状の彫刻が可能です:
Q.加工にはどのようなレーザー技術が使われていますか?
A.一般的なタイプには、CO2、固体(Nd:レーザ)、色素レーザ、エキシマレーザ、YAGレーザ、ファイバーレーザレーザがあります。マルチキロワットファイバーレーザーは、ポータブルで高性能です。
Q.レーザー加工できる材料の種類は?
A.金属、非金属を問わず、鉄鋼からプラスチック、木材、セラミックス、グラファイトの複合材まで、あらゆる素材の加工が可能です。
Q.レーザー加工のメリットは何ですか?
A.非接触の非熱加工、高精度、高精度を実現します。その他の利点として、機械振動が少なく、工具の摩耗がなく、複雑な3Dパーツの加工がパーツ固定なしで可能です。