Descubra cómo las tecnologías de vanguardia, la precisión y la eficacia dieron forma a la aparición de la tecnología CNC con Control Numérico por Ordenador. Examine la tendencia, las ventajas y las perspectivas de futuro en la industria del fresado.
Tecnología CNC: Cómo la forma completa CNC está revolucionando la fabricación moderna
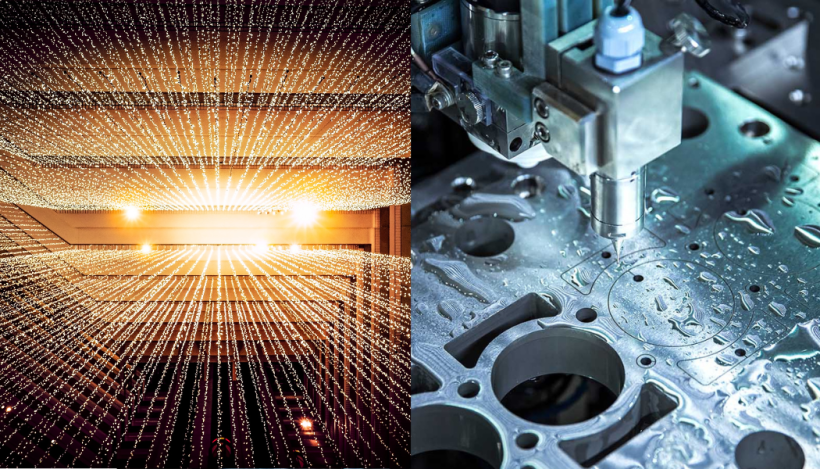
¿Qué es el CNC?
El CNC, o Control Numérico por Ordenador, era una nueva tecnología revolucionaria para la fabricación. Mecanizado CNC trata de la automatización de máquinas-herramienta mediante una programación informática precisa.
Las máquinas CNC siguen esencialmente las instrucciones codificadas para cortar, dar forma o grabar materiales con una precisión y consistencia inigualables. Su capacidad para automatizar tareas complejas ha sido una herramienta esencial para las industrias modernas, desde la aeroespacial hasta la electrónica de consumo. Para apreciar el papel que la tecnología CNC ha desempeñado en la fabricación, es importante comprender la forma completa del CNC. Ha unido la artesanía tradicional y la tecnología moderna para crear diseños innovadores y procesos de producción eficientes.
Importancia del CNC en la fabricación
El paso de la fabricación manual a la automática es un cambio de juego. La tecnología CNC ha sustituido las formas que requieren mucha mano de obra por una solución automatizada y ha aumentado la velocidad y la eficacia de muchos procesos. Esta tecnología puede garantizar una mayor precisión, libre de errores humanos, y menos tiempo en la línea de producción, lo que la hace indispensable para las industrias que requieren una producción de alta calidad. Tanto si se trata de la producción de un prototipo como de miles de componentes, el CNC ha establecido un nuevo punto de referencia sobre lo que es posible en la fabricación.
Los orígenes de la tecnología CNC Historia
El CNC partió del mecanizado manual, que requería operarios cualificados para manejar las máquinas mediante operaciones manuales. Después llegaron las máquinas semiautomáticas, en las que era necesaria una intervención humana parcial. A principios de la década de 1940 se produjo un gran avance con la invención de los primeros sistemas de tecnología CNC, que utilizaban cintas perforadas para programar las máquinas. Esa innovación dio origen a la fabricación automatizada moderna.
Primeros retos
A pesar de su promesa, la primera tecnología CNC tenía varios retos. Estaba limitada por la escasa potencia de cálculo y los costes de las máquinas y las herramientas de programación eran demasiado elevados para su implantación. Además, los fabricantes tradicionales no estaban dispuestos a utilizar un sistema que requería conocimientos y formación específicos. Desarrollo de la tecnología CNC
Avances tecnológicos La tecnología actual se distingue enormemente del CNC convencional. El control de la máquina se mejora mediante la incorporación de controladores lógicos programables (PLC) específicos y el uso exclusivo de software CAD/CAM permite transiciones del diseño a la producción sin interferencias. Estos avances hacen que los sistemas CNC sean más fáciles de usar y versátiles
Tipos de máquinas CNC
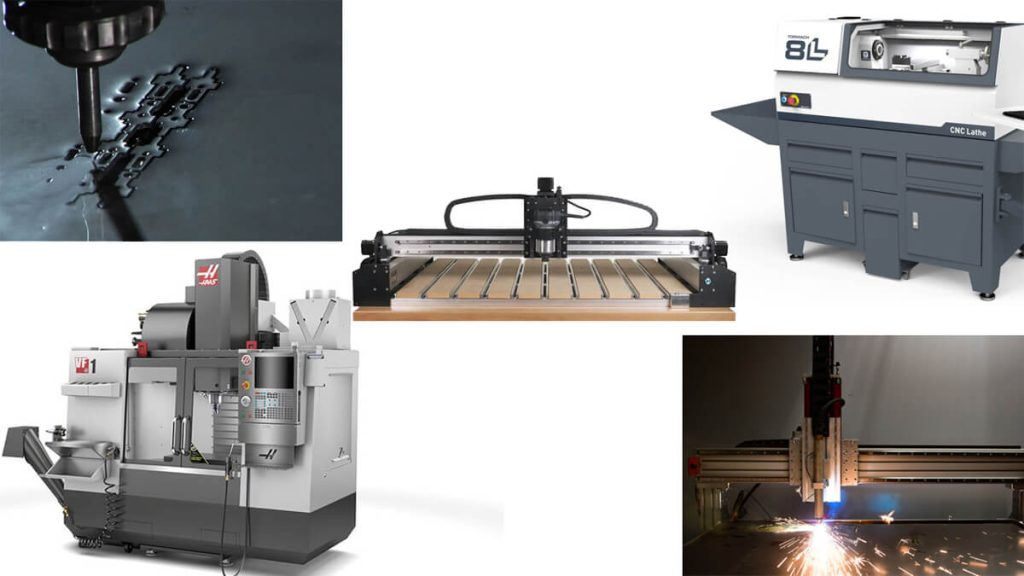
- Fresadoras CNC-Se trata de una máquina, cuyo mecanismo corta y da forma mediante el corte de múltiples ejes.
- Torno CNC es una herramienta de maquinaria utilizada para crear piezas de trabajo que sean cilíndricas. Su funcionamiento se basa en un principio de corte rotacional.
- Cortadora de plasma-La máquina corta metales a muy altas temperaturas mediante plasma.
- Cortadoras láser Cortar metal con gran precisión utilizando rayos láser focalizados.
- Otros tipos avanzados de máquinas son las impresoras 3D y las cortadoras por chorro de agua. Ahora son posibles técnicas de fabricación innovadoras.
Avances clave
Hoy en día, la tecnología CNC cuenta con un mecanizado multieje que permite diseños y formas sofisticados. El CNC inteligente con IoT permite la supervisión en tiempo real y el funcionamiento a distancia, aportando la máxima eficiencia y precisión al proceso.
La forma en que el corte CNC ha impactado en las industrias Mayor precisión y exactitud Las máquinas CNC son muy precisas, alcanzan niveles de micras, manteniendo así la calidad en la producción en masa. Este nivel de precisión es fundamental para los dispositivos aeroespaciales y médicos, donde los pequeños errores pueden tener graves consecuencias.
Tiempos de producción más rápidos gracias a la automatización de tareas repetitivas, la tecnología CNC reduce drásticamente los tiempos de producción. Esto es muy vital para industrias como la automoción y la electrónica, donde la velocidad importa para satisfacer las demandas del mercado. Reducción del desperdicio de material
El CNC optimiza las trayectorias de corte, permitiendo así un desperdicio mínimo de materiales, lo que hace que el proceso de fabricación sea menos costoso e incluso respetuoso con el medio ambiente. Avanzado CAD/CAM El software garantiza la máxima eficiencia en el uso del material.
Personalización y versatilidad
Las máquinas CNC son buenas con una amplia gama de materiales, desde metales hasta plásticos y compuestos. Es gracias a esta flexibilidad que se puede conseguir fácilmente la creación rápida de prototipos y la personalización basada en las necesidades particulares de diversas industrias y clientes.
El papel de las herramientas CNC en la industria moderna
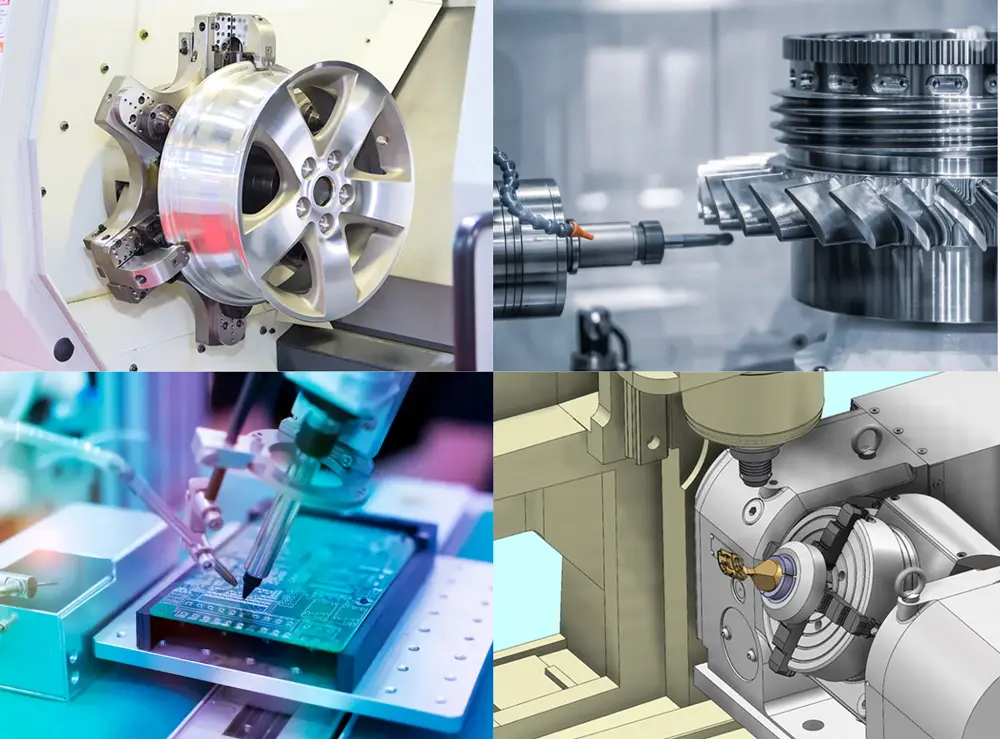
Tipos de herramientas CNC Se utilizan varias herramientas para lograr la función principal de las máquinas de tecnología CNC. Las herramientas de corte como fresas, brocas y escariadores son muy vitales para cortar y dar forma al material de manera precisa .Las herramientas no cortantes como las herramientas de palpado y los portaherramientas garantizan mediciones precisas y la sujeción segura de las herramientas. Las herramientas especializadas diseñadas para determinados materiales o aplicaciones amplían aún más la versatilidad de los sistemas CNC.
Materiales para herramientas CNC
El material de la herramienta es uno de los principales factores que afectan al rendimiento y la durabilidad. Los materiales de las herramientas de HSS son conocidos por su tenacidad y versatilidad, lo que los hace muy adecuados para la mayoría de las aplicaciones. Las herramientas de metal duro ofrecen más rendimiento de corte y mayor longevidad, especialmente en operaciones de alta velocidad. Para usos específicos, se utilizan herramientas diamantadas y cerámicas con una dureza y resistencia al desgaste sin igual, ideales para cortar materiales abrasivos.
Mantenimiento y longevidad
La inspección periódica de las herramientas de tecnología CNC es esencial para su rendimiento óptimo. Las mejoras en los sistemas de monitorización y predicción de la vida útil de las herramientas permiten predecir mejor el desgaste y programar las sustituciones a tiempo. Estos avances reducen el tiempo de inactividad y alargan la vida de las costosas herramientas, marcando así una diferencia en la rentabilidad.
Ventajas del CNC para los fabricantes
Eficiencia de costes
El coste de la inversión en tecnología CNC es bastante elevado en las fases iniciales. Aunque puede llevar tiempo, los ahorros a largo plazo son sustanciales. La automatización evita depender en gran medida de mano de obra cualificada, reduce los costes operativos y evita el desperdicio de materiales por errores.
Escalabilidad
Los sistemas CNC ofrecen una flexibilidad sin parangón en la industria. Los fabricantes pueden alternar entre la producción de lotes pequeños y las operaciones a gran escala sin grandes complicaciones. Esta adaptabilidad es especialmente beneficiosa para las industrias con demandas fluctuantes.
Seguridad mejorada:
El Máquina CNC reduce la implicación humana que puede tener lugar en operaciones de mecanizado arriesgadas. Además, las funciones de seguridad integradas ayudan a minimizar los accidentes, aumentando así la seguridad de las personas en el lugar de trabajo.
Competitividad internacional
La tecnología CNC permite fabricar con estándares internacionales en términos de precisión y calidad. Esta característica se hace necesaria en la arena competitiva de los mercados mundiales y mantiene la competitividad en una industria en rápida evolución.
Retos y limitaciones
Costes iniciales elevados
El coste inicial de la compra de máquinas CNC y otras infraestructuras es muy caro, especialmente para las pequeñas empresas. Además, la necesidad de programadores y operarios cualificados aumenta el coste.
Dependencia tecnológica
Los sistemas CNC están fijados con una tecnología importante y como tal producen un alto riesgo de cierre en caso de avería del sistema. Se necesitan actualizaciones constantes y que el personal reciba formación continua para familiarizarse con las últimas tecnologías, lo que resulta caro.
Preocupaciones medioambientales
Los procesos CNC suelen consumir mucha energía, lo que plantea problemas de impacto medioambiental. La eliminación de los fluidos de corte y los materiales de desecho es otro reto que hay que abordar para garantizar la sostenibilidad.
El futuro de la tecnología CNC
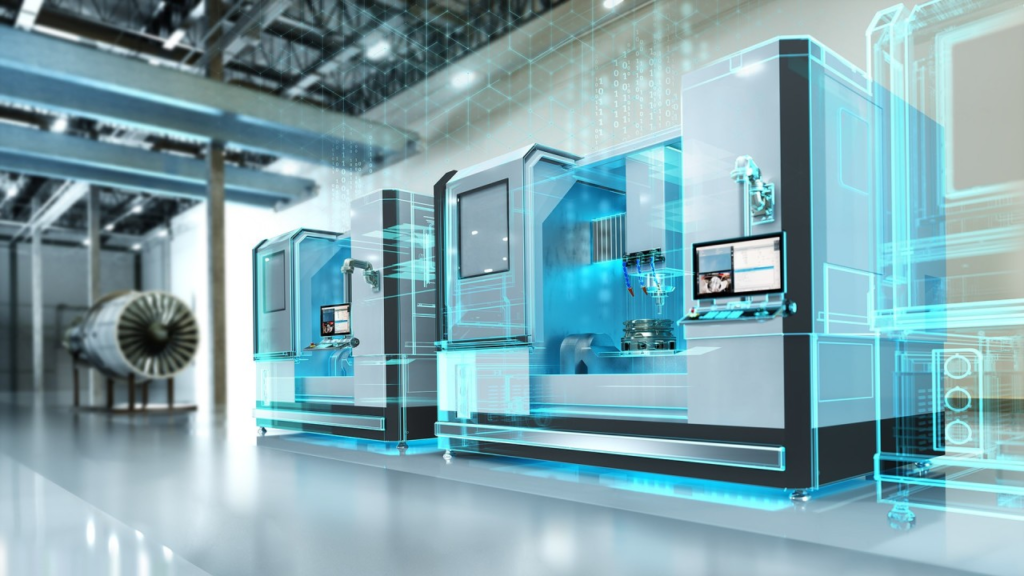
Tendencias emergentes
El futuro del CNC está determinado por las innovaciones que incluyen sistemas impulsados por IA y técnicas de fabricación aditiva que se integran en Corte CNC. Las máquinas híbridas que combinan el corte CNC con procesos aditivos ya están creando olas en la industria.
Innovaciones potenciales
Las máquinas CNC sostenibles y eficientes desde el punto de vista energético se están convirtiendo en un elemento imprescindible a medida que las industrias buscan reducir su huella ecológica. Incluso pueden preverse sistemas de autoaprendizaje que dependan menos de la intervención humana, lo que promete otra oleada de cambios para la fabricación.
Implicaciones para la industria
Estas innovaciones se extenderán por todas partes, impulsando la competitividad de la fabricación mundial y ofreciendo nuevas oportunidades en sectores de alta tecnología. A medida que la tecnología CNC siga evolucionando, aumentará el impacto que tendrá en las industrias y las economías.
Conclusión
Los cambios en el desarrollo de la tecnología CNC cambiarán el panorama de una industria manufacturera con velocidades, precisión y flexibilidad polifacética sin precedentes en ella. Desde la fase inicial del mecanizado manual hasta los sistemas totalmente automatizados de los últimos tiempos, el CNC ha revolucionado una y otra vez las formas de romper los límites anteriores de lo que realmente se podía producir. Con tareas que son altamente complejas y producidas en masa con sólo unos pocos errores, esto se ha convertido en una herramienta muy central para que los fabricantes tengan una oportunidad de satisfacer esas demandas del mundo moderno.
A pesar de estos inconvenientes -incluidos los elevados costes iniciales y las preocupaciones medioambientales-, las ventajas del CNC sobre sus homólogos se mantienen firmes: rentabilidad, escalabilidad y mayor seguridad. Además, se siguen desarrollando innovaciones en los materiales de las herramientas, sistemas inteligentes y máquinas híbridas, lo que promete un futuro en el que la tecnología CNC esté más disponible y sea más sostenible y eficiente que nunca.
Con el avance hacia la era de la cuarta revolución industrial, también denominada Industria 4.0, el CNC seguirá siendo un componente importante para definir el futuro de la fabricación en todo el mundo. Esta flexibilidad de adaptación a las nuevas tecnologías y a las demandas del mercado garantiza su aplicabilidad en los años venideros. Para cualquier empresario que desee seguir siendo relevante y adoptar la última tecnología en su línea de producción, el CNC no puede ser ignorado.
Preguntas frecuentes
1. ¿Qué es el CNC y por qué es importante?
CNC significa Control Numérico por Ordenador. Es vital en la fabricación de procesos de automatización con gran precisión y eficacia, cambiando el mundo en su conjunto.
2. ¿Qué tipos de herramientas tienen las máquinas CNC?
Herramientas de corte que suelen ser fresas y brocas, herramientas no cortantes como las de palpado, y herramientas especiales para manipular diversos materiales.
3. ¿Cómo ha cambiado la tecnología CNC con el tiempo?
El CNC ha evolucionado desde el mecanizado manual hasta los sistemas impulsados por IA con funciones avanzadas como el mecanizado multieje y la integración de IoT, mejorando la productividad y la innovación.