It is no exaggeration to state that the art of precise boring with the help of CNC machining technology is one of the key ingredients of efficiency within this significantly complex area. This practical and informative manual covers crucial concepts and recommendations that will improve CNC boring operations and help achieve extraordinary results in all manufacturing projects.
Understanding CNC Boring Operations
CNC milling technology has slowly but not yet introduced a drastic change in the manufacturing process, as it now allows for the shaping of its elements with little human input. CNC Boring Operations particularly entails increasing the size of already existing openings or holes in materials to precise dimensions, which is necessary in industries that use complex parts.
Advanced Techniques for CNC Boring
1. Optimal Machine Shop Setup
The requirement of setting up a well-equipped machine shop is always considered the basic starting point for achieving optimum utilization of CNC boring operations. A CNC-machining-specific machine shop makes it easier to have all the proper materials and tools required for the proper functioning of a CNC workshop. Some of the factors to be considered include where the floor space of the store would be located and how workbenches and CNC lathes, among others, are to be positioned.
CNC lathes have been widely used in small metal CNC machining for performing various functions, especially when dealing with delicate components. From this point of view, manufacturers are now able to improve their machinabilities by acquiring and installing CNC lathes of the highest technological standard, which enables the economical production of products with accurate dimensions and surface finishes.
2. Tool Selection and Optimization
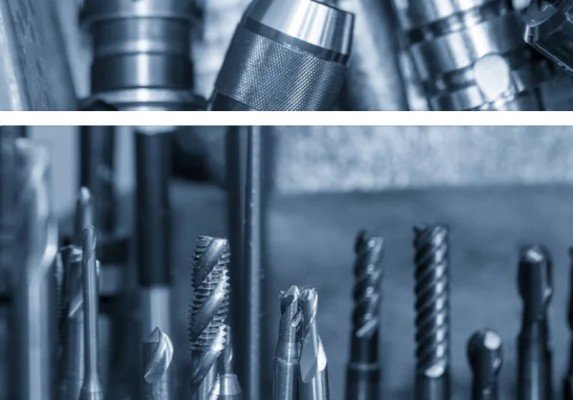
The proper choice of cutting tools significantly affects the efficiency of operations related to computer numerical control CNC boring operations. For example, diamond-tipped boring bars are widely recommended for machining through hardened materials, primarily attributed to their high hardness and approved large wear resistance. These tools not only increase the life expectancy of the tool but also maintain a steady output all through the machining cycle.
Sized CNC boring operations heads help in allowing for different bore sizes as they do not need to be adjusted frequently, which also helps in minimizing operating time. In addition, utilizing enhanced coatings and tool geometry adaptation in cutting tools for specific applications boosts total efficiency and the tool’s durability.
3. Optimized Cutting Parameters
Cutting parameters, like cutting speeds and feed rates, should be well adjusted to ensure that the company gets the best results from the machines. However, through the utilization of these CNC lathes, the above parameters can be fine-tuned to correspond with the nature of the material and the corresponding machining needed, hence improving efficiency and accuracy.
Continuing the CNC boring operations for a very long time also requires good dimensional accuracy that is why the application of more complex strategies of controlling chips is also crucial. Peck drilling and high pressure coolant systems are used to control the generation and removal of the chips which in turn cause interrupted machining and enhanced surface finish.
Also, it is important to use CNC programming such as G code and simulation for checking the right tool path and also efficient time for completing machining difficult parts. Through such a preventive measure, the organizational effectiveness is increased while at the same time minimizing the errors made in manufacturing.
4. Advanced Toolpath Strategies
Strategies for toolpath are some of the most important strategies that will cause the CNC boring operations and enhanced machining results. Techniques like helical interpolation can therefore allow for gentle and continuous material removal, and there is very low vibration of the tool and a very good surface finish.
Algorithms targeted at toolpath are tailored to the characteristics of the materials being worked upon and the geometry of the part, which increases the efficiency of the machining process and the overall quality of the final product. G02 The application of tool paths which are customized to the magnitude of machining demands makes it possible for producers to boost the efficiency of cutting while sweeping under the excess usage of energy and time on the machinery.
activation of multi-axis machining in the tooling of CNC boring operations allows the creation of complex shapes and intricate forms with the highest level of accuracy. The fact that such novel types of parts can be manufactured also broadens horizons of possibilities in manufacturing and, at the same time, increases versatility and contending force of CNC machining.
5. Integration of Cutting Fluids and Lubricants
Thus, cutting fluids and lubricants are used actively in the context of improving CNC machining and tool performance. For example, the high-performance coolant system allows for efficient cooling of heat generated during the machining processes, thus preventing tools from overheating and premature deterioration.
Introducing appropriate cutting fluids will necessitate the choice of specific cutting fluids that uphold particular material needs and desired machining features concerning chip removal. These cutting fluids help in minimizing tool wear, which in turn contributes to efficiency and effectiveness of the CNC boring operations by improving the surface finish quality.
Sustainability is now part of modern manufacturing practices; the utilization of recycled cutting fluids as well as the improved management of environmental impact reflect the broad areas in which the firm is committed to operations efficiency and the environment.
Benefits of Implementing Advanced Techniques
- Enhanced Precision and Accuracy: It is to this end that this paper aims at discussing how tight tolerance and dimensions are important in achieving dimensions that are desirable in current applications of manufacturing.
- Increased Efficiency and Productivity: Efficiencies in the usage of CNC lathes and related machining services minimize lead times, increase throughputs, and increase production yield.
- Cost Efficiency: Reducing scrap rates, fluctuations in tool costs, and production losses due to machine maintenance boosts the efficiency of manufacturing.
Conclusion
It is crucial for machine shops that want to focus on precision manufacturing to develop their knowledge of the complex methods of using computer numerical control in the CNC boring operations process. Through adopting CNC machining technology, choosing the right material, and applying new lathe processing technology, manufacturers are able to improve their advanced machines and fulfill new requirements from contemporary advanced industries.