Emerging Role of CNC Machining for Automotive Industry
As a technology that is over half a century old, CNC machining has had a significant impact on the automotive industry since the adoption of the methodology. CNC technology originated in the aerospace industry and coursed its way to automotive due to its versatility and ability to deliver accuracy, fast and consistent. The shift from manual machining process to CNC machining, was a landmark step which allowed superior accurate and intricate work to be made this paved way for manufacture of complicated parts. CNC machining has come a long way over the years, is even used more today with a better software and better machines, is and always has been an important part of the automobile industry.
CNC Machining for Prototyping used in the automotive industry
prototyping has been an important activity in the automotive industry where engineers fashion sections of the automobile to fit, for the purpose of trying them out to see if they would make the desired impression on the full-scale automobile after assembly. In this area, CNC machining stands out as a great boon for the production of accurate prototypes in the shorter time possible and at a low cost. Key prototypes in the automotive industry include:Key prototypes in the automotive industry include:
1. Engine Components
CNC is useful in building prototypes of parts for engines for reference such as;
- Cylinder heads
- Intake manifolds
- Camshafts
Such components demand a high degree of accuracy in the manufacturing process for greater effectiveness, reliability and increased engine performance.
2. Transmission Parts
A lot of the original equipment for transmissions, including:
Is developed through CNC machining. Manufacturing precision is a key parameter in these applications, as these parts should be able to perform under rigors of real road use and specified tolerance levels.
3. Suspension Systems
There are different suspension components, which can be produced using CNC machining services. These include:
- Control arms
- Shock absorbers
- Struts
These prototypes must be accurate and durable in terms of precision to support the required performance of automobiles for control and security.
4. Brake Systems
During the prototyping,
- The brake calipers
- Rotors
- Brake pads
Can be shaped through computer numerical controlled machining. Small variations help the engineers create larger prototypes that meet the need for efficient braking and safety.
Custom automotive parts using CNC Machining
There is increasingly more emphasis on individual differences as many people want automobiles that are designed according to their tastes. CNC machining allows for manufacturing specialty parts that reflect consumers’ needful characteristics. From processes that involve creating custom alloy wheels, custom exhausts or parts in the interior of the car, CNC machining is the best process for achieving quality customization solutions such as;
Custom Wheels
Advanced technology in manufacturing through CNC machining helps automakers in developing special designs of wheels which can be used to meet clients’ individuality at an extended level. This is because CNC machines can accurately maneuver to consistent dimensions to allow the manufacturing of wheels that have the right measure of performance and looks.
Performance Exhaust Systems
Custom exhaust parts are produced using CNC machining technology; this boosts the performance and head turning rumble of vehicles. Lowered exhaust systems can enhance the efficiency of Automotive Industry engines and include a unique audio track.
Interior Trim
Dashboard, shift knob, trim and others can be machined out of a number of materials Custom interior parts include dashboard panels, gear shifters or other trim parts which can be made of a number of types of materials. The components have to be well-fitted and the CNC machining helps in achieving the desired fit and finish for interior components that give the vehicle a stylish look.
What are Common Materials for Automotive CNC Machined Parts?
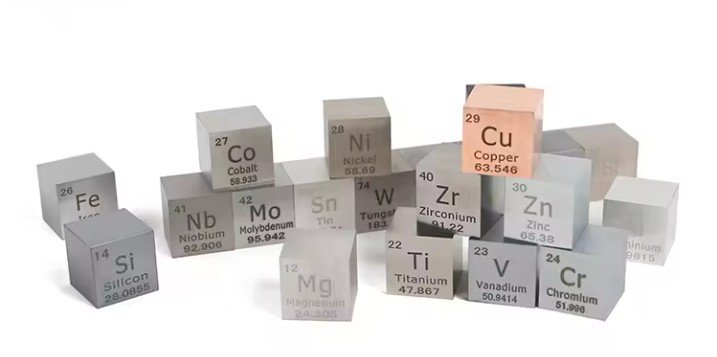
In the automotive industry, it is used in manufacturing a variety of parts made of diverse materials through the usage of custom CNC machining services. One of the most important and influential factors for selecting material is the particular mechanical properties that are required for the specific part like strength, durability, weight, thermal stability, etc. Here are some of the primary materials used in CNC machining for the automotive industry:Here are some of the primary materials used in CNC machining for the automotive industry:
알루미늄
- Properties: Some of the properties includes; Light weight, high strength to weight ratio, ease in machining, and corrosion resistance.
- Applications: Compression, cylinder head, piston, transmission, wheels, suspension and any other automotive industry part that is made from cast iron.
Steel
- Properties: The materials thus used should have high strength, elongation, hardness and wear resistance. Offered in a range of grades such as carbon steel, alloy steel or Stainless steel.
- Applications: Some of the parts likely to be in need of relaying are gears, shafts, bearings, chassis and other structural parts.
티타늄
- Properties: Superior strength and rigidity, low density, corrosion resistance, and heat resistance were other advantages of the material.
- Applications: High performance automotive industry engine parts, exhaust systems and aerospace application quality vehicle parts.
Magnesium
- Properties: Although, complex and thin-walled structures are made from it, it has a very high strength-to-weight ratio and is easily machinable.
- Applications: Vehicle body, bony structures, and all areas where engineers demands for low weight is prioritized.
Brass and Copper
- Properties: Still on the mechanical properties; excellent on machinability, outstanding on corrosion and good electrical conductivity.
- Applications: Analgesic, antirheumatic and anti-inflammatory preparations; electrical connectors, fittings, and parts having decorative functions.
플라스틱
Acrylic (PMMA)
- Properties: Good transmission of light through the covers, good tensile strength, and resistance towards UV light.
- Applications: Lenses, covers, and illuminator parts.
폴리카보네이트(PC)
- Properties: It has a high impact strength, thermal stability, and even translucency at some levels.
- Applications: Door, headlamp covers as well as interior panels and safety related parts.
Polyethylene (PE)
- Properties: It also has other great features such as its ability to withstand most chemical environments, high capacity for impact, and low coefficient of friction.
- Applications: Fuel tanks, fluid containers, and protective covers – all of these need to be best possible for the target audience.
Nylon (PA)
- Properties: Practical advantages: very high strength, superior wear resistance, and relatively good chemical resistance.
- Applications: Main engine bearings, main engine bushings, gears, and fasteners.
폴리프로필렌(PP)
- Properties: Fatigue resistance, tough to chemicals and light in weight.
- Applications: Organ, systems, batteries, cases, and trims are some of the interior parts and the parts located under the hoods.
Composites
Carbon Fiber Reinforced Polymer (CFRP)
- Properties: Another advantage of carbon fiber reinforced polymer composites is that they possess very high specific strength to density, high stiffness, and moderate thermal stability.
- Applications: For this purpose, car manufacturing organizations utilize body panels, structural bodies and high-performance parts in their sports and luxury car productions.
Glass Fibre Reinforced Plastic (GFRP)
- Properties: There are several benefits attached to this product, and they include high strength, good impact resistance, and comparatively reduced weight.
- Applications: engl( Body parts included the engine, gears, bonnet, boot, and bumper while the interior had the dashboard, doors, roof, seats and wheels.
Ceramics
Silicon Carbide (SiC)
- Properties: High hardness, good thermal stability and better wear resistance are some of the features that makes this type of coating very useful.
- Applications: Fluids; brakes; high-performance brake discs; engines; engine components; and wear-resistant parts.
Aluminum Oxide (Alumina)
- Properties: It has high hardness, conducting heat effectively while also being a good electrical insulator.
- Applications: Electrical insulators in power plants, sensors boxes and any high temperature uses.
Exotic Alloys
Inconel
- Properties: Oxidation and corrosion resistance at high temperatures, high strength at higher temperatures, and therefore better thermal stability compared to most of the metals.
- Applications: Turbocharger parts, exhaust valves among others are located in exposed areas that subject them to harsh conditions.
Monel
- Properties: It also has very good percent of corrosion resistance, high strength as well as dispatching toughness.
- Applications: Other components include fuels and water tanks, exhaust systems, and other marine based equipment parts.
Advancements in CNC Machining for Automotive Applications
The advances in the application of CNC machining technology today means more benefits to the automotive industry especially in terms of productions. Advancements in software, tools and machines have further advanced possibilities of CNC machining, and thus there already upgrades to efficiency and quality in automotive production.
Multi-Axis Machining
Most current CNC machines are available with numerous axes, meaning various orientations of parts to create highly intricate components are achievable in a single operation. This has the advantages of making it efficient in terms of time and accurate in producing complicated designs of automotive industry parts and components.
Additive Manufacturing Integration
CNC or Computer Numerical Control is the integration between machining and guide to 3D printing, in which hybrid parts can be produced. This method results to the combine the benefits of both the technologies in terms of weight of the components and structural reinforcement.
Advanced Materials
CNC machining has increased its coverage across different types of material such as high strength alloy materials, composite, and ceramic. These materials have better physical and mechanical properties for automotive industry components which include enhanced toughness and light weight.
Automated Quality Control
Enhancing the Quality Control process through the implementation of walkways and creating direct connections with CNC machining ensures that each component is manufactured to the utmost quality standards. Monitoring and inspecting Probes t loss leads to enhanced product quality and a reduced risk of defects related to real-time operations.
Sustainability and CNC Machining in the Automotive Industry
After analyzing all possibilities that are faced in today’s rapidly growing automotive industry, it can be concluded that CNC machining is a very viable solution to many problems when it comes to environmental control. Advanced CNC machining techniques contribute to sustainability in several ways:
Material Efficiency
CNC machining cutting operation is efficient as it does not require chopping or raw shaping of the components from a large block of material. This has a further advantage of lowering resource use, costs, and, in general, the social impact on resources within the environment.
Energy Efficiency
Traditional cnc machines were relatively powerful since they used a lot of energy when they were on the operation as compared to the modern CNC machines. This enabled a decrease in energy consumption, which has directly resulted in less greenhouse gas emission and overall cost of operation.
Recyclability
Substrate materials utilized in CNC machining include metal or some types of plastic, and typically, these can be recycled. For instance, this makes it possible for materials to be recycled and used again which can also have equally minimized the effects on the environment.
Lightweighting
CNC machining allows for lightweight parts not only to be realized but to be created without any properties being sacrificed in the process. This means that lighter vehicles consume less energy to make them run implying that they are eco friendly as they produce less emissions to the atmosphere.
The Future of CNC Machining in the Automotive Industry
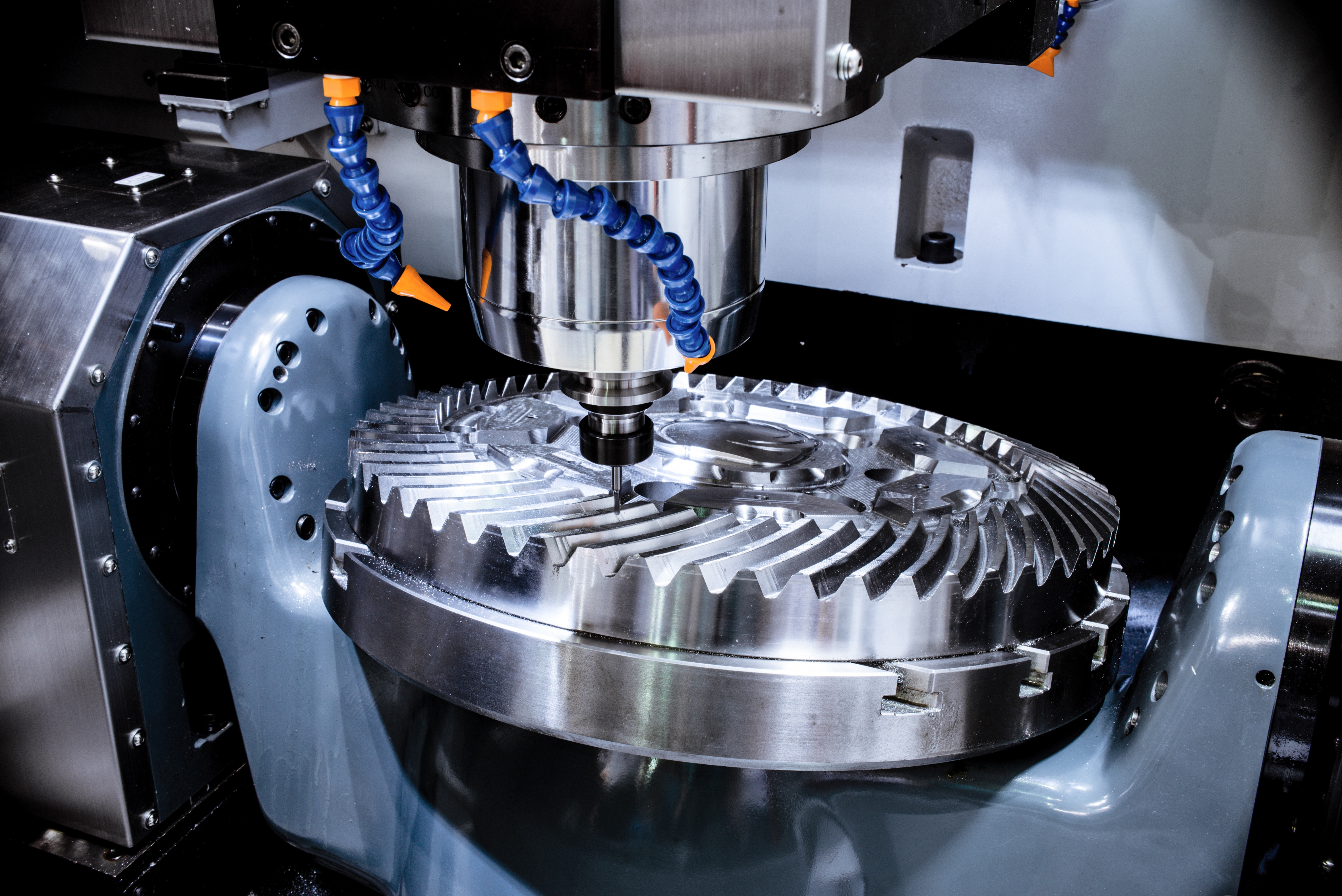
In the future, more developments can be expected of the CNC machining techniques and it remains a crucial player in the worldwide Automotive Industry business. Several trends and innovations are likely to shape the future of CNC machining for automotive applications:Several trends and innovations are likely to shape the future of CNC machining for automotive applications:
Industry 4.0 Integration
CNC machining with industry 4.0: This paper seeks to analyze how CNC machining has integrated with industry 4.0 applications like the Internet of Things (IoT), Artificial intelligence (AI), etc will include new technologies to advance production competency. CNC machines integrated into smart factories will also sustain the ability to feed data in real-time, supporting advanced analysis for predictive maintenance and monitoring, therefore avoiding congestions of productive assets.
Electrification and Autonomous Vehicles
New types of components required by electric and Automotive Industry vehicles shall be expected to flourish in the market. CNC machining will be crucial in creating molds for prototyping and building components in electric drivetrain assemblies and other assemblies like the battery systems, and sensor casings.
Customization and On-Demand Manufacturing
This means the trend for customization is set to remain strong, supported by CNC machining that allows making parts for specific customers only. Rapid and cost-efficient prototyping will help to design as well as manufacture specialized elements of computer and machinery.
Sustainability Initiatives
CNC machining would prove to be a driving force in contributing towards the improvement and furtherance of sustainable ventures in the automotive industry manufacturing sector. Increasing trends in material science and the technology of machining will also help in reducing the effect on the environment and pave way for establishing automobile that has minimal effects on the environment.
Summary
In the automotive industry, Computer Numerical Control, CNC for short, machining has been adopted as a crucial technology to contribute to new forms of development of the structure in the industry. From prototype creation and design variation to changes in technology and the promotion of sustainability, the application of CNC machining remains revolutionary for the automotive industry. CNC machining however will stay as an important innovation within the auto industry as it helps design refined and sophisticated types of automobiles that cater to the changing market and the environmental consciousness of consumers
MXY: An expert in the field of automotive CNC machining
As one of the leading automotive industry CNC machining enterprises, MXY is dedicated to making the dream come true to deliver the best automotive project with extraordinary accuracy and short cycle time.
MXY goes on to claim corporate clientele, which comprises of renowned car manufacturers such as: Mercedeme Benz, Audi, GMC, Toyota and Porsche among them. Due to the high level of synchronization between the various operating axes in our 3-, 4-, 5, and 9-axis CNC machining centres, we are able to offer the top-notch components to these industrial giants at a reasonable price.
In case you fail to reach us, allow us to demonstrate to you how MXY can be the vehicle to the success of your project. If you would like more information, please check our CNC machining and CNC machined parts.