レーザー切断がどのように変わるかをご覧ください。 金属加工 比類のない精度と効率でレーザーの種類、主要なパラメータ、高度な技術、自動車や航空宇宙などの産業にわたる複雑な設計を形成する技術をご覧ください。
金属加工におけるレーザー切断:複雑なデザインのための精密技術

この記事では、金属加工におけるレーザー切断の包括的な概要を取り上げ、その意義とさまざまな産業での応用について紹介します。レーザー切断がどのように機能するのか、基本原理とCNCシステムの役割について詳しく説明します。その後、CO2レーザ、ファイバーレーザ、ダイレクトダイオードレーザなど、金属切断に使用されるさまざまな種類のレーザについて説明します。レーザ出力、切断速度、ビーム焦点距離、ガス圧、パルス周波数設定などの主要な加工パラメータについて、最適な結果を得るための重要性を検証します。
この記事では、高精度の利点を強調しています。 金属加工 レーザー切断を通して、比類のない精度、バリのないきれいな切断、後処理の必要性の低減を強調しています。レーザー技術が、多軸加工、複雑な中空形状、マスカスタマイゼーションなど、複雑な金属設計の作成をどのように可能にするかを探求します。また、レーザー技術の進歩について、新たなレーザー光源、高度な機械構造、切断技術に焦点を当てて説明します。
様々な産業におけるレーザー切断の用途を概説し、その多様性を示す具体的な使用例を紹介します。結論では、製造業におけるレーザー切断の将来と産業プロセスへの影響について考察しています。最後に、FAQのセクションでレーザー切断技術に関する一般的な質問を取り上げています。
金属のレーザー切断
レーザー切断は、集束したレーザーピラーを使用して、さまざまなシートメタルをスライスし、多面的なプランを作成する、非常に正確で柔軟な金属加工方法です。驚異的な精度と熟練度で切断を行うことで、レーザー切断は企業全体の組み立て工程を変え、驚異的な加工を可能にしました。 金属部品.
レーザー切断の仕組み
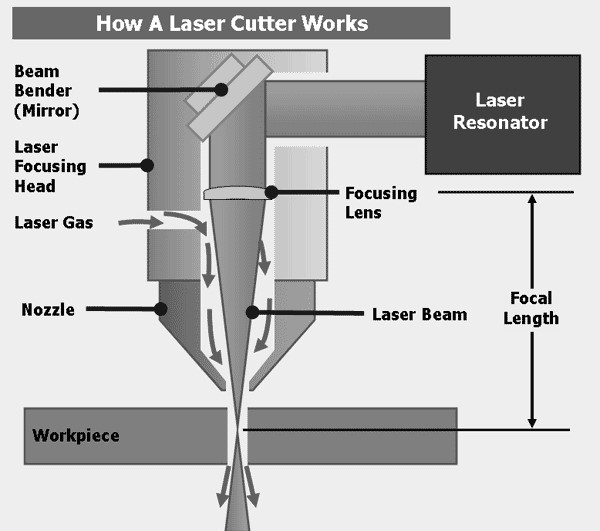
レーザー切断は、一般的にCO2レーザーやファイバーレーザーの集光レーザービームを、ミラーやレンズを通して金属表面に照射します。3000℃を超える高熱が発生し、目的の切断経路に沿って金属を溶融または蒸発させます。酸素や窒素のようなアシストガスの流れが、よりきれいな切断のために溶融くずを取り除きます。一方、コンピュータ数値制御(CNC)システムは、切断ヘッドの動きとレーザー出力を正確に管理し、ミクロンレベルの精度で詳細な設計を正確に順守します。
使用されるレーザーの種類
異なるレーザー光源は、必要な用途に応じて金属切断に定期的に使用されます。CO2レーザーは、金属によって消費されるすべての周りに赤外線を放射し、中程度の厚さの穏やかな鋼、アルミニウムおよび非鉄金属の切断のために強化されています。ファイバーレーザーは、処理された鋼やより細いチェックの切断に理想的な高出力密度を伝える超密度のシャフトを生成します。Nd:YAGレーザーは、金や銀のような壊れやすい金属を扱うのに適した赤外線または明るいレーザー光を生成するためにネオジムドープ貴石極を使用しています。ダイレクトダイオードレーザも同様に、適応可能な金属加工アプリケーションの保証を示しています。
主要プロセスパラメータ
特定の金属の種類と厚さに基づいて設定する必要がある重要なパラメータには、レーザー出力、切断速度、ビーム焦点距離、ガス圧、パルス周波数設定が含まれます。これらの変数を適切に調整することで、サイクル速度や消耗品使用量などのスループット要因のバランスを取りながら、各生産実行を通じて一貫した部品形状とエッジ品質を確保します。プロセスの最適化は、加工精度と効率を維持するために金属材料やゲージを切り替える際にも不可欠です。
精密金属加工
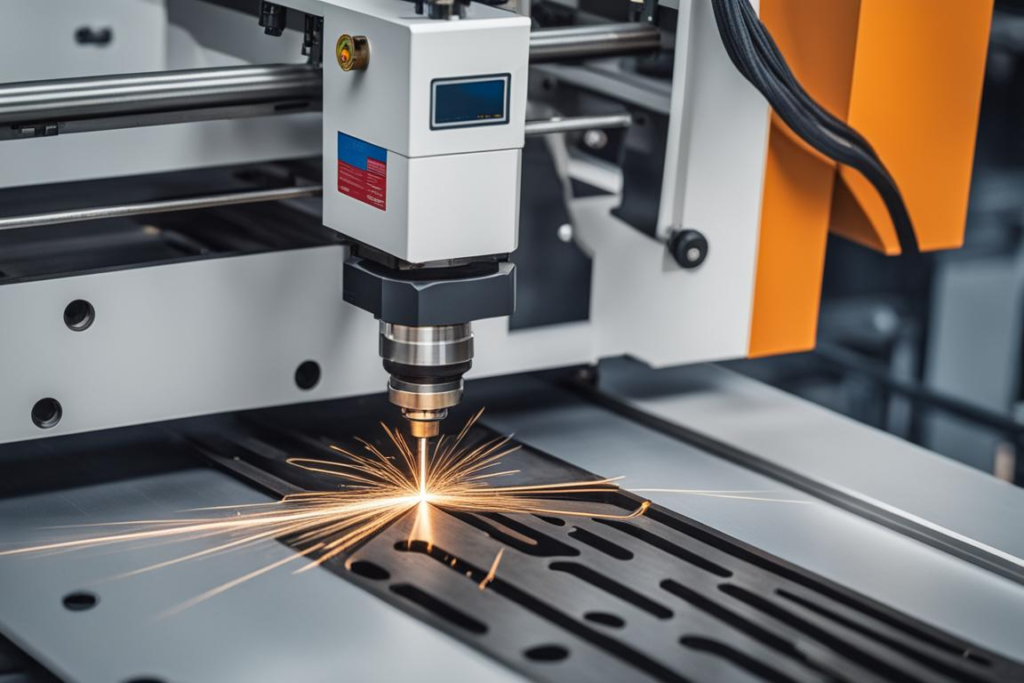
レーザー切断は、予測不可能な計画や複雑な数学的形状を作成する能力を通じて、金属加工において既に考えられないほど高い精度を達成することを生産者に促します。レーザーの革新とPCの数学的制御(CNC)は、予測不可能な金属部品やパーツの組み立て能力をひっくり返しました。
比類のない精度
レーザー切断の主な利点の1つは、その卓越した精度と再現性、そして厳しい公差能力です。ピンポイントに集光された微細なレーザービームは、ミクロン公差内の配置再現性を達成することができます。このレベルの精度は、密に詰まった特徴、小さな穴、スロット、シームレスにかみ合う挿入物を持つ部品の製造を可能にします。医療機器、電子機器、航空産業などの業界では、機械的な装置やシステムを組み立てるために、複数の極小切断部品間のミクロン公差を維持するレーザー切断の能力に依存しています。設計特徴にわたって一貫した±0.005mmの精度を確立することで、複雑なアセンブリやサブアセンブリを構築することができます。
バリのないクリーンカット
レーザー切断の特徴は、熱影響部を最小限に抑えてバリのないエッジを作り出すことです。レーザーエネルギーは高度に集束されているため、周囲の加工物を溶かしたり損傷させたりすることなく、金属の薄い切り口を加熱して蒸発させることができます。その結果、切断エッジは、二次的なバリ取り工程を必要としない、ほとんど研磨されたような外観になります。滑らかなエッジは、下流の品質管理手順と完成品の美観に役立ち、お客様は加工後の労力と検査コストを節約できます。医療用インプラントの場合、バリのないエッジは、製造中に滅菌された部品を汚染するリスクを低減します。
後処理の軽減
エッジ仕上げ工程を省くだけでなく、レーザー切断は溶接、研削、サンディングなどの作業の要件を削減します。ビームから直接得られるきれいな幾何学的形状は、設計公差を危険にさらす可能性のある追加の製造工程による歪みを最小限に抑えます。これらの利点が相まって、精度が向上し、製造ワークフローが加速し、完成部品の品質を低下させる誤った偏差の導入が阻止されます。
複雑な金属デザイン
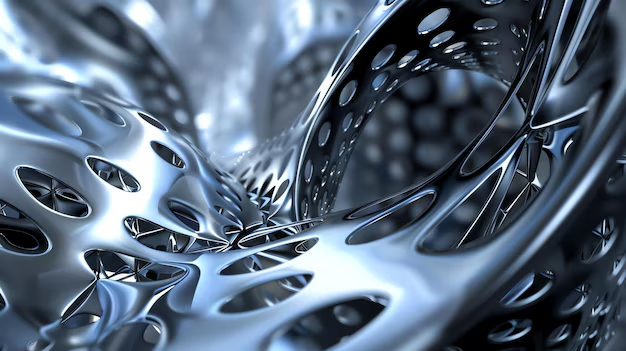
精密レーザー技術とコンピュータ制御システムの融合は、複雑なディテールを持つ幾何学的に複雑な金属部品を製造するための新たな可能性を解き放ちました。CNCマシンの器用なプログラミングと連動するレーザーは、従来の製造方法の能力をはるかに超えて製造設計の範囲を拡大します。
多軸加工
回転軸を装備した先進的なレーザー切断システムは、さまざまな方向からワークピースを横切るレーザービームの反復的なスキャンを可能にします。調整された軸の動きとプログラムされたレーザーシーケンスにより、複雑な表面形状を持つ3D中空形状も製造可能になります。医療用インプラント、タービンブレード、金型およびダイは、標準的な平らなストック操作では達成できない自己完結型の形状を作成するレーザー切断の能力の恩恵を受けます。多面彫刻およびプロファイリングにより、複雑な内部空洞内のすべての露出面に、均等に分散された詳細パターンまたはマイクロテキストを追加できます。
複雑な中空形状
デジタル設計に従ってプレカットされた金属ブランクを入れ子にしたり積み重ねたりすることで、精巧な容器、筐体、複雑な内部空洞を持つ幾何学的立体を自己組み立てすることができます。レーザー切断されたインターロックとアンカーを使用した入念に配列されたレイヤーの製造により、きめ細かな特徴を持つインレットベルマウスを備えたタービンハウジングのような製品が得られます。ネスティングソフトウェアは、材料の使用量を最適化し、レーザー切断工程でのスクラップを最小限に抑えながら、積み重ねられた層間の部品登録を調整します。複数の内部平面と密に詰まったフィーチャーを持つ複雑な中空形状は、製造を合理化します。
マス・カスタマイゼーション
プログラマブル・レーザーは、顧客の仕様に応じて多様なデザインを迅速に切り替えることを可能にします。レーザー切断パラメータ調整だけで標準的な構成ブロックを操作することにより、ハードな金型投資なしで、少量で完全にカスタマイズされた最終使用部品のジャストインタイム製造が可能になります。マスカスタムレーザ製造は、家電製品から医療機器まで、これまでにない自由な設計を可能にします。
レーザー加工技術
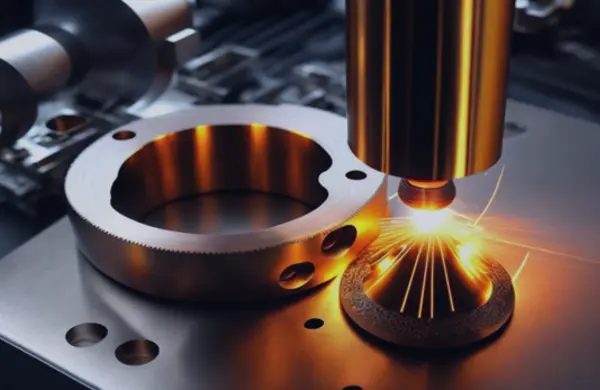
レーザ光源技術と製造プロセス制御戦略の継続的な進歩は、レーザベースの加工能力を徐々に変化させています。革命的な技術革新は、レーザーが重要な役割を果たす産業アプリケーションの範囲を広げています。
レーザー光源の進歩
ハイパワー・ダイレクト・ダイオード・デバイスのような新しいレーザーは、従来のCO2レーザーに比べてエネルギー変換効率が向上し、運用コストの削減が期待できます。また、波長の多様性により、新しい材料の加工が可能になるかもしれません。ファイバーレーザー技術は、同時に、より高速な動作、より微細な形状解像度のためのより小さな集光スポット、およびメンテナンスフリーの長い動作時間を実現します。工作機械との統合により、加工コストが削減されます。超高速パルスファイバーレーザーおよびダイレクトダイオードレーザーは、従来のナノ秒レーザー(1 ns = 10^-9 s)に対して、フェムト秒(1 fs = 10^-15 s)で測定される超短赤外または紫外パルスを生成します。これらのレーザは、熱影響部(HAZ)のない精密な材料加工を実現します。数キロワットの出力は、セラミック、先端合金、ダイヤモンドのような以前は困難であった高熱負荷材料を加工するために、競合技術の強みを凌駕するようになりました。
高度なマシン・アーキテクチャ
統合されたロボットにより、部品のマニピュレーション、検査、ロード/アンロードのワークフローを完全に自動化できます。マルチレーザーアレイは、1回のスキャンで大面積のシートを切断する高出力ビームを合成します。クラウド製造プラットフォームを介してネットワーク化された分散型レーザー加工ステーションにより、遠隔地の製造センターでレーザー加工能力を拡張できます。光コヒーレンストモグラフィのような工程内計測による品質監視は、リアルタイムで偏差アラートを生成します。レーザーとアディティブを組み合わせたハイブリッドマシンは、設計の自由度をさらに広げます。このような革新的な技術革新により、生産コストを削減する一方で、達成可能な精度を向上させ、あらゆる産業における新たな川下アプリケーションを満たします。
高度な切断技術
レーザーシステムの絶え間ない進歩と関連するプロセスパラメータの改良が、新たな製造能力を引き出しています。特殊な材料や超小型コンポーネントに最適化された新しいレーザー操作方法は、レーザー技術アプリケーションの境界を広げています。
超短パルスレーザー加工
兆分の1秒(10^-15秒)で測定される超短光パルスを活用するフェムト秒レーザーは、熱の影響をほとんど受けずにターゲット表面を正確にアブレーションします。大きな熱影響部を発生させることなく、これらのレーザーは熱に敏感な物質から繊細なマイクロ光学部品や医療用インプラントを製造します。エッチング中にメルトゾーンが発生しないため、以前は不可能であった透明材料のパターニングも可能です。それに応じて、フェムト秒レーザーの微細切断の生物医学的応用が盛んになります。
特殊素材の冷間切断
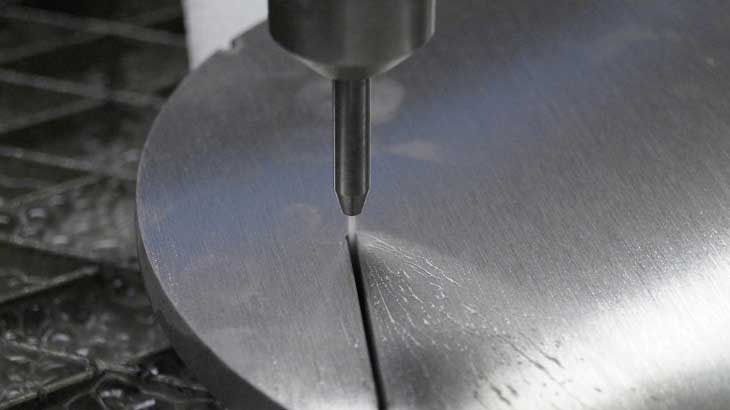
マイクロメートルスケールの極めてタイトなガウシアンビームウェイストは、通常のレーザー出力密度を超えるため、炭素繊維複合材料、プラスチック、サーモトロピック液晶ポリマー(LCP)の構造的完全性を損なうことなく、ネットシェイプ加工を可能にします。低熱負荷加工は、疲労、衝撃、腐食に強い堅牢な航空宇宙構造要素の材料特性を維持します。マイクロエレクトロニクスにおいても、新たな小型化のフロンティアが出現しています。
ガイドビーム照射
複雑な部品形状は、かつては全反射ベースのビームルーティングを妨げていました。現在では、ファイバー、流体、グラディエントインデックスレンズにより、レーザーエネルギーを障害物の周囲に流し、複雑な内部形状を加工することができます。ビーム位置安定装置はミクロン単位の忠実度を保証します。ガイドウェーブ技術は、光導波路を使用して、フットプリントなしでレーザービームを発信する遠隔ネットワーク操作レーザー製造プラットフォームを加速します。統合されたプロセス計測が偏差を追跡します。
マルチビームの組み合わせ
同期化された超高速レーザーアレイは、個々の出力を効果的に組み合わせ、通常のピーク出力能力をはるかに超える複合ビームを生成します。熱溶融溶接継手のニアネットシェイプ・マイクロマシニングやそれ以上の加工は、今や電子ビームに取って代わる野望を実現します。これらの画期的な技術は、高精度レーザの動作範囲を拡大し続け、厳しい材料組成制御と微細化の要求に依存する産業全体の新たなフロンティアに対応します。絶え間ない進化は、レーザー加工の優位性を保証します。
結論
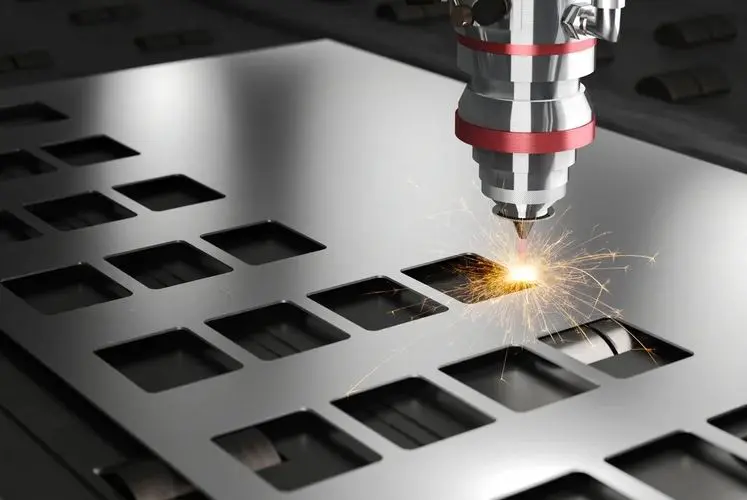
レーザー切断は、機器とソフトウェアの継続的な進歩に支えられ、その精度、適応性、生産性によって金属加工に革命をもたらしました。この技術は、基本的なシート切断から高度な多軸加工まで、複雑なアプリケーションの製造プロセスを強化し、新しい製品設計を可能にし、生産を合理化します。また、超高速加工や遠隔レーザー照射など、さまざまな特殊技術により、その可能性はさらに広がっています。自動化、ビッグデータ、クラウドベースの製造が普及するにつれ、レーザー切断は、スマート工場における効率、品質、管理を向上させながら、業界全体の複雑な設計要件に対応し、近代的な製造の中心であり続ける態勢を整えています。その絶え間ない革新は、レーザー切断が世界の産業進歩と経済成長を推進するための重要な技術としての役割を確固たるものにしています。
よくあるご質問
Q: レーザーカッターは何を切断できますか?
A: レーザー切断は、従来の切断と同様に、木材、プラスチック、複合材料、芸術的な質感など、多くの材料に適用できます。いくつかの適切な構成要素に関する属性には、温かみのある特性、厚さ、反射率が含まれます。
Q: レーザーカットの精度はどのような変数によって決まりますか?
A: レーザーの出力と周波数、中心長の設定、切断速度、ヘルプガスの張力と種類などが切断精度に影響します。材料の厚さも精度に影響します。高出力レーザーは、概して、よりタイトな弾力性で動作します。
Q:レーザー切断は、選択的金属加工技術とどのように対照的ですか?
A:プラズマ切断の方が大量切断には早い場合もありますが、レーザー切断の方がより厳しい抵抗を伝え、熱の影響を抑えることができます。ウォータージェット切断は、より広範な材料に対応できますが、正確さとペースは劣ります。切断のような機械的サイクルは、レーザー手順の精度のマークを逃します。
Q: レーザー切断にはどのような用途がありますか?
A: レーザー切断は、予測不可能な例や小さな開口部、複雑な3D計算が必要なガジェット、臨床機器、航空、自動車、その他の事業で成功しています。通常のモデルには、隅、タービンの鋭角、PCB、改良品、義肢などが含まれます。
Q:レーザー切断では、どのような安全対策を講じる必要がありますか?
A: 管理者は常につま先の閉じた靴を履き、健康眼鏡をかけ、防護服を着るべきです。レーザーは目や体への負担が大きいため、機械には連動したウェルビーイング・モニターが必要です。十分な換気は有害な排気を排除し、企業はレーザー・ウェルビーイングの準備をする必要があります。
Q: レーザー切断の費用はどのように決められますか?
A: 主な費用要因には、材料の種類/厚さ、部品の複雑さ、必要な抵抗、作成量、および後処理の必要性が含まれます。ギヤの能力と評価モデルについて考えるために、さまざまなレーザー切断工場から明細書を要求してください。