Injection molding Products is a manufacturing process, by which molten chips, usually plastic or metal are injected into a mold. The process continues until the material reaches the cooling stage and solidifies into the mold cavity shape. Injection molding is a fantastic choice if you want to benefit the mass production of complex details or if you have a limited amount of budget.
Detailed description of the injection molding products
- Injection molding process
- Material used in the manufacturing
- Industries and applications which use injection mold parts
- Introductory part of advantages of this manufacturing method over others
Whether you would like to personalized Injection molding Products for your custom parts in plastic or metal for a product you manufacture, or just want to get more information on how this process is being done.
Versatility and Applications of Injection Molding
Injection molding Products is used for the production of plastic parts that range from bottle caps to airplane avionics enclosures.
Injection molding is especially versatile as it is used to produce a wide range of plastic and metal parts across all industries. Some of the most common injection molded products include:
- Plastic bottles and packaging, too.
- Vehicle dashboards, grilles, door silhouettes, and instrument clusters are the features.
- Medical devices and worker properly.
- These components, along with capacitors, inductors, resistors, and diodes, are grouped together in electronic enclosures.
- This equipment consists of several electronic modules and a power supply.
- Accessories, Sporting goods, camping equipment.
- Needless to say, item’s range is not limited to household ones, such as storage boxes, cutlery and furniture.
- The enclosures and the internal components of the appliances.
In brief, any part that is required to be made precisely, at speed and at scale using low cost tooling then is an ideal candidate for Injection molding Products process. This can be done in a high precision level to meet exact specifications, from delicate parts with fine details, complex geometries and thin walls with tight tolerances.
Business approach
Plastic and metal injection molding:
step-by-step process
1. The tool is made first of all as CNC machined part, out of a tool steel model which is based on 3D CAD models for the part. The injection mold is, in principle, a Injection molding Products that consists of two main components, i.e. negative imprint of the part and a core which shapes outside.
2. Freshly produced feed of either plastic particulate or metal powder is force-fed through the gravity into the injection molding products machine by the barrel heater. The solid material is heated until it melts into the liquid state.
3. Through heavy pressure, the injection nozzle then uses speed to force the material under an injection mold tool at great speed, filling any mold tool cavity.
4. Mold cooling is done via water running through it or by being left to cool using ambient temperature. This leads to the solidifying of the molten feedstock and taking on the shape of the mold.
5. Finally, the mold is supposed to be solid enough which might allow the postion of the parting line and the extraction of the finished injection molded parts. Cycle is now continued for the next part.
Injection Molding Plastic Types
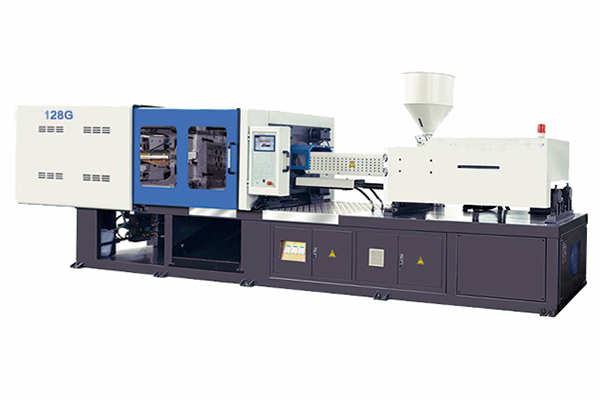
A variety of Injection Molding Products plastic materials are tens of that make up, allowing companies to select one that has the required balance of mechanical, thermal, electric and aesthetic properties needed for each application. Some of the most common plastic types used are:
- Acrylonitrile Butadiene Styrene (ABS): It has got the reputation of being strong, durable, and highly resistant to impact. It’s used for the making of cars parts, toys and appliance housings.
- Polypropylene (PP): High flexural resistance does not fail under bending, strong chemical/heat resistance and high melting point. It has a wide range of applications in the industry. For example, it’s used for the manufacture of tubes for various goods,from production parts to decorative items, bottle caps, medical devices, packaging, and so much more.
- Polyethylene (PE): Polyethylene offers high capacity to resist corrosion, lower friction and in fact, it’s relatively inexpensive. Normally used for bottles, containers, washers, spacers, seals and tubing that are made from these materials.
- Polycarbonate (PC): Its main virtue is the strength and durability. The molecular structure of this material guarantees high heat and impact resistance. used for making of optical lenses, transparent components, medical devices, automotive parts as well as frames for electronic devices.
- Acetal and POM: Are of high mechanical strength, low friction coefficient and dimensional stability under the effects of load.. Could be applied to agents, gears, latches, fasteners, valve bodies and sprinkler system agents.
Injection Molding Metal Materials
However, plastic injection molding products is responsible for a larger percentage of usage and metal injection molding (MIM) is widely accepted as another great method to create small metal parts in big quantities.
Common MIM metals include:
- Stainless steel: Its highly strength and corrosion resistance properties with the amazing thermal properties, are the most valuable. It covers a wide variety of applications such as medical instruments and valves, gears, springs, and orthopedic and dental implants.
- Low alloy steel: Yield strength much higher and is also more convenient to magnetize. Used for locking mechanisms, gears, and surgeon tool parts and metallic molds.
- Soft magnetic alloys: These materials consist of elements like nickel, cobalt,iron and silicon, which can be induced to magnetize easily. Use in electric motors, rotors, starters, solenoids, breaker core components and other.
- Aluminum: Lightweight with excellent thermal conductivity and corrosion resistance. Widely used in automotive parts, aerospace structures, and consumer electronics housings.
- Magnesium : The lightest structural metal with a good strength-to-weight ratio. Used in automotive, aerospace, and electronic device components for weight reduction.
- Titanium: High strength, lightweight, and excellent corrosion resistance. Ideal for aerospace parts, medical implants, and high-performance automotive components.
- Copper: Excellent electrical and thermal conductivity. Commonly used in electrical connectors, heat exchangers, and plumbing fittings.
- Zinc: Low melting point and excellent corrosion resistance. Often used for die-casting small components, automotive parts, and household hardware.
- Nickel Alloys: High strength, heat resistance, and corrosion resistance. Used in turbine blades, aircraft parts, and chemical processing equipment.
- Brass: An alloy of copper and zinc, known for its machinability and corrosion resistance. Used in plumbing fittings, decorative hardware, and musical instruments.
- Bronze: An alloy of copper and tin, known for its toughness and resistance to wear and corrosion. Commonly used in bearings, bushings, and marine hardware.
- Tool Steel: High hardness and wear resistance, ideal for cutting and machining tools, molds, and dies.
Industries are the Dominant Market for Injection molded Parts

We should note that injection molding products has become a brand new technique to fabricate plastic and metal components with the aid of which many different applications both in plastic and metal industry are possible. Below are some of the primary examples:Below are some of the primary examples:
- Industria automobilistica: Interior parts such as dashboards, door panels, center consoles and instrument clusters in addition to exterior elements like side mirrors, emblems, bumpers and skid plates can be tailored to customer’s needs.
- Medical Industry: Surgical instruments, testing equipment housing, device handles and grips, disposable syringes and cartridges, orthopedic implants, and other medical products.
- Consumers Goods: Homemade products, electronic shells, power tools, toys, sports equipment, gardening supplies, furniture pieces, and undoubtedly many more goods.
- Industrial Manufacturing: Gears, rollers, joints, conveyor components, pneumatic system parts, means of transportation devices, bolts, bushings and bearings which are used in all kinds of machines and tools.
Benefits of injection molding products
There are multiple reasons injection molding products is one of the most ubiquitous manufacturing processes across industries, including:There are multiple reasons injection molding is one of the most ubiquitous manufacturing processes across industries, including:
1. High degree of planar and parallelism and hence the manufacture of very complex shapes and details of detail.
2. The enormous savings in materials through accurate injection fluid management that prevents waste or spillage is surely noticeable.
3. Serialization and uniformity made it possible to manufacture thousands of quality parts in an hour from each mould.
4. Low labor need since the injection molding products machines from the time the process is started, most of the action is being automated.
5. Great advantages such as the versatility of using various types of material, surfaces, inserts, and post-finishing processes.
6. Particularly, low tooling costs and hence the injection molding is so cost-effective technique at the production scale of volume.
7. The possibility of making consolidated sub-assemblies and completed products, which can be integrated or packed later, more accessible.
If you fabricate components at least to some degree, do not hesitate no more and let away others ahead of you, for the process of injection molding products cannot be outdone. It is the last but not the least revolution that modern mass production across all the industries is based on. Thanks to the introduction of this technique the quality, efficiency and economics is improved.
Summary
Injection molding products is proven to be the most efficient way to produce additional plastic and metal components as there is a rigid process for precision, repeatability, and lower costs. If your project needs a polymer plastic enclosure to be able to sustain an electrically sensitive electronic device or impact resistance enclosure on a man-powered device that is made of polymer materials, injection molding products process offers a suitable solution.
This manufacturing process will have a wide impact on all and sphere of production both at home, industries and institutions, and hence these injection molded parts will be occupying our living-rooms, vehicles, factories and hospitals for a long time to come.