Discover how high-speed CNC machining is achieving ultra-precision in industries like aerospace, medical devices, and electronics. Learn about the future of precision manufacturing with advanced CNC systems and tools.
Achieving Ultra-Precision with High-Speed CNC Machining

Is ultra-precision manufacturing the future of the production system? In this article, we will look at how manufacturers are using high-speed CNC machining techniques. We will also see how to elevate sophistication and precision by using cnc machining and how this technology is used to meet the strict tolerances of industries across the globe in the years to come.
Ultra-precision machining
Ultra-precision machining, therefore, can be described as manufacturing that uses processes to create parts of high precision with tolerances in the micron/nanometer scale. This is done using tools that include cutting tools that are suitable for the type of workpiece or material to be cut and most times requires special cutting techniques in a bid to achieve tight tolerances and smooth surface finishes. Ultra-precision machining is thus a manufacturing process that emphasizes high accuracy in the creation of small features and tight tolerances for specialized operations.
Key characteristics of ultra-precision machining
Some aspects of ultra-precision machining include applying complex 3-D profiling through integrated multiple spindle and 5-axis CNC machining services. There are special tools available in order to counter the effects of the environment such as temperature, noise, and vibrations that affect the accuracy. Precise metrology equipment is also needed to inspect ultra-fine detail machining. A range of exotic and difficult-to-machine materials can be processed to exacting levels of precision.
Applications that require ultra-precision machining
Some of the industries that use ultra-precision machining include aerospace industry, healthcare industry, electronics industry and the energy industry. These include parts of aircrafts, artificial limbs and joints, chips for semiconductor manufacturing, equipment and components of accelerators. New product development and many other areas of manufacturing also use this technology for prototyping of the parts and other complex designs that are required to be very precise. Low tolerances are essential for applications where the reliability of the equipment and its performance cannot be compromised.
High-speed CNC machining

Definition and overview of high-speed CNC machining
High-speed CNC machining involves leveraging advanced CNC systems, control designs and cutting tools to rapidly remove material from a workpiece at far greater feeds and speeds than traditional machining. These new capabilities enable processing components up to an order of magnitude faster without compromising precision or part quality.
Benefits of high-speed machining over traditional machining
The benefits of high-speed CNC machining include increased productivity through higher throughput as well as efficiency gains from reduced cycle times. Part accuracy is maintained while minimizing heat generation issues at the tool-work interface. Combined with the latest CAM software, complex geometries can now be achieved with tighter tolerances. Overall production costs per part are decreased.
Industries utilizing high-speed CNC machining
Aircraft parts manufacturers were early adopters due to economic motivations to slash production lead times. Automotive now employs high-speed CNC machining centers extensively for high-volume production. Industries like medical devices and electronics utilize the technology for its precision and flexibility benefits. Even mold making has been transformed through high-speed machining of mold components.
The relationship between CNC technology and precision manufacturing
Role of CNC in precision manufacturing
Guide to CNC Machining forms the basis of most modern precision manufacturing techniques. Precisely controlling axes through coded programming facilitates best-in-class repeatability and accuracy unattainable through manual means. Complex profiles can now be cut in various materials to dimensions measuring millionths of a meter.
Impact of CNC on machining accuracy and tolerances
Tightly integrated feedback loops between the control system and machine tool help remove human inconsistency as a factor limiting precision. Through automated compensation for thermal effects, backlash, and other variances, parts can easily meet demanding tolerances of +/- 2-3 microns or better. Complex equations also enable optimal cutter path planning.
How CNC enables complex profiling and ultra-fine machining
The programmable flexibility of CNC revolutionized the machining of sculpted geometries in tool and die applications. Today, multi-axis machining centers equipped with high-speed CNC machining spindles support ultra-fine profiling on near-surface features measuring hundreds of millimeters or smaller. Industries like medical implants depend on this fine detail capability.
Achieving ultra-precision with advanced CNC systems
Importance of automation, spindles, and controls
To reach the tightest tolerances, automation removes human inconsistency from the process. High-speed CNC machiningspindles with advanced motors paired with direct-drive technology minimize backlash variation. Controls featuring direct-torque feedback loops provide 0.1 micrometer positioning repeatability under changing thermal conditions.
Factors like temperature, vibration, and noise control
Stability is critical, so modern systems incorporate sealed enclosures pressurized with oil mist or nitrogen gas. Air bearings or granite beds minimize machine deflection under cutting forces. Sensors detect resonant frequencies to be filtered from the structure. Active damping of vibration approaching the workpiece is key to ultra-precise finishes.
Capabilities of modern high-speed CNC systems
State-of-the-art systems feature 5 or even 6-axis simultaneous interpolation for sculpting complex freeform surfaces. Performance monitoring and feedback optimize the cutter for the material being processed. Systems achieve ±1μm accuracy on workpieces measuring 1m long. Tolerance is maintained through real-time compensation of thermal expansion effects.
High-speed machining techniques for precision components
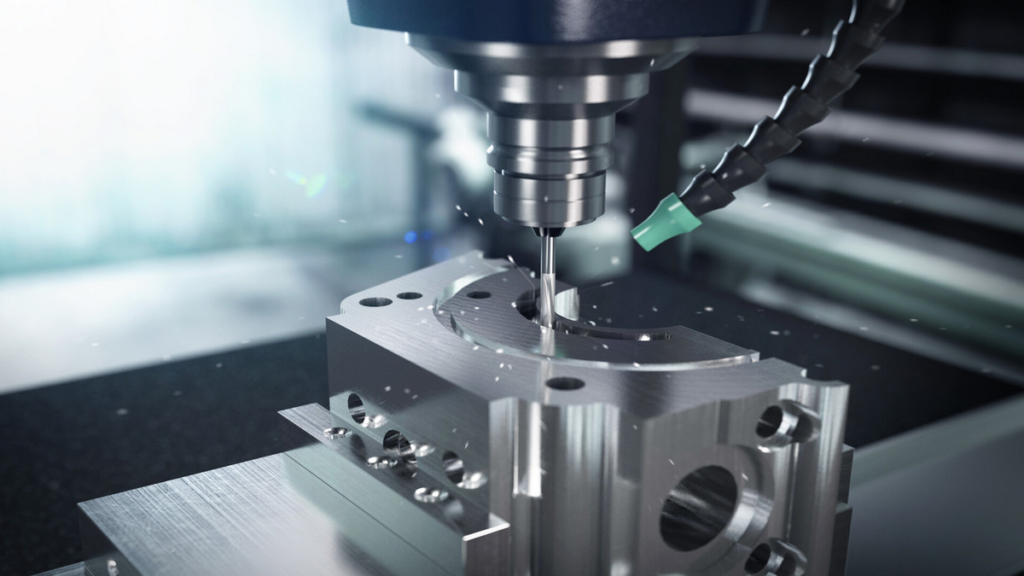
Micro-machining, ultra-fine machining, and laser machining
Techniques like micro-turning and micro-milling use specialized miniaturized tooling to shape intricate micrometer-scale structures. Laser high-speed CNC machining also supports the milling of fine subsurface features through ablation. Together these methods create microfluidic chips, medical implants, and other precision components.
Employing high-speed tools and cutters
To fully leverage advanced systems, machine tools require refined cutters featuring optimal materials, geometries and coatings. Diamond-tipped and self-sharpening tools maintain edge acuity during screeding at 5000 SFM or beyond. Tools minimize process forces and chatter for superior finishes.
Optimizing techniques like high-speed cutting
Achieving precision demands optimizing high-speed CNC machining techniques like dynamic and regenerative milling. Processors adjust pitch, tilt, and depth dynamically for each pass. Coolants are tailored to protect both the edge and substrate. Cutting parameters are fine-tuned to prevent deflection yet maximize metal removal rates for production efficiency.
Maximizing efficiency with high-speed spindles and tools
Benefits of high-speed spindles in CNC machining
Spindles capable of 25,000+ RPM with associated direct-drive motors eliminate lost motion from belt drives. Air bearings provide frictionless support for torques exceeding 300 Nm. Together this allows drastically faster material removal while maintaining surface integrity.
Developments in tooling technology
Advances include coated solid carbide tools, polycrystalline diamond tools, and tools brazed with cubic boron nitride. Rotating tool holders boost radial rigidity to avoid deflection at high speeds. Tool path strategies keep cutting edges engaged for maximum chip loads.
Importance of tool choice and machining parameters
Chip thinning tendency and material hardness dictate optimal geometries, coatings, and cutting parameters. Factors like feed per tooth, spindle power, and cutting fluid selection impact achievable metal removal rates, tool life, and finished part quality. Processors carefully evaluate all variables for maximum efficiency.
Future of achieving ultra-precision
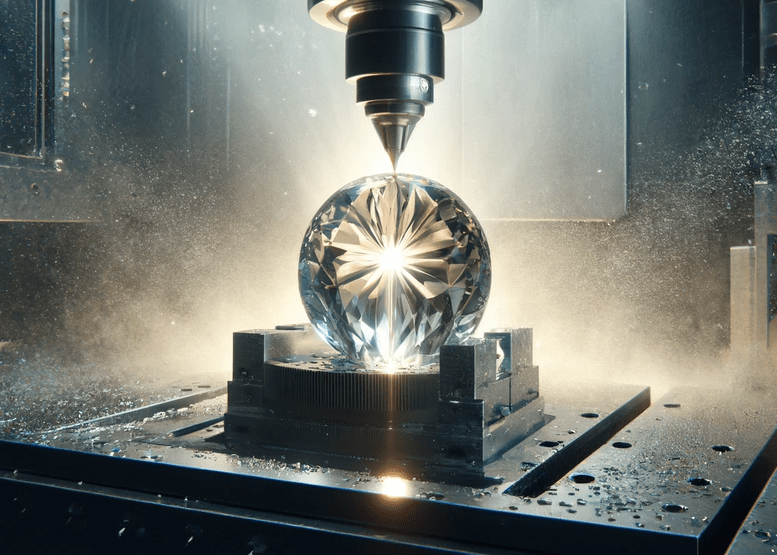
Continued CNC and tooling advancements
Advances will include high-rigidity parallel kinematic designs for 6-axis systems. Multi-axis spindles offer rotary-driven tools. New carbide micro grain technologies boost tool life. Integrated metrology inspects cuts in-situ. Coatings like aluminum CNC machining titanium nitride push adhesion limits. Data analytics helps maximize process parameters.
Growing applications in industries like medical and aerospace
Demand is fueled by miniaturized mechanical components for medical devices. Implants require chemical purity and biocompatibility during fabrication. Aerospace adopts new alloys machinable only through ultra-precision techniques. Consumer products rely on micro-optics established via high-precision high-speed CNC machining.
Role of automation, robotics, and additive manufacturing
Automation enables 24/7 manufacturing cells for high-mix low-volume production. Robotics combines CNC machining with assembly. Additive manufacturing improves part consolidation for reduced setup complexity. Hybrid systems leverage each technology’s strengths for newly possible part geometries.
In conclusion, high-speed CNC machining utilizing the latest systems and tools enables manufacturers to achieve previously unattainable levels of precision, efficiency, and part quality. Combining high-speed machining techniques with advanced automation will be key to addressing demands across industries that rely on ultra-precision manufacturing.
Conclusion

In conclusion, the integration of high-speed machining capabilities with advanced CNC systems has revolutionized precision manufacturing. No longer constrained by the limitations of traditional techniques, manufacturers can now routinely produce complex components with micron-level accuracy and repeatability. As applications continue pushing the boundaries of miniaturization, complexity and quality, the marriage between ultra-fast machining and highly automated high-speed CNC machining opens up new possibilities. Leveraging the latest in tooling, metrology and process intelligence will be pivotal for industries heavily reliant on ultra-precision to meet technical demands well into the future.
FAQs
What industries benefit most from ultra-precision machining?
Industries like aerospace, medical devices, electronics and energy benefit greatly due to their reliance on precisely machined components. Even prototyping across all industries leverages the technology for iterative testing of complex part designs.
How do advanced CNC systems enable higher precision?
Features like auto-compensation for thermal effects, direct-drive motors and multi-axis simultaneous movement provide tighter control over miniscule deviations. Automation also removes human inconsistencies, allowing precision to within microns or smaller tolerances.
What breakthroughs are improving CNC machining efficiency?
Advances in spindle technology now support speeds exceeding 25,000 RPM for drastically faster material removal. New cutting tools featuring improved geometry, grain structure and coatings minimize heat generation at the cutting edge for faster feeds and speeds.
How will CNC machining evolve to address future needs?
Continued development of parallel kinematics, multi-axis spindles and integrated metrology will push CNC capabilities. Data analytics will optimize machining parameters for specific parts. Hybrid manufacturing leveraging additive and high-precision subtractive techniques will realize unprecedented levels of complexity and precision.