Découvrez des solutions efficaces aux problèmes courants de fabrication des métaux, y compris les techniques de soudage et de découpage. Apprenez la préparation des matériaux, la configuration de l'équipement, l'automatisation et bien d'autres choses encore pour obtenir des résultats cohérents et de haute qualité dans le domaine du travail des métaux.
Résolution des problèmes liés à la fabrication des métaux : Mieux pour les techniques de soudage et de coupage

La fabrication de métaux joue un rôle essentiel dans des secteurs tels que l'automobile, l'aérospatiale et l'industrie manufacturière. Les fabricants coupent, plient, soudent et transforment les matières premières en composants et structures précis. Cependant.., fabrication de tôles peut présenter des difficultés : les coupes peuvent être imparfaites, les soudures peuvent présenter des défauts et les travaux peuvent subir des retards. Les problèmes sont dus à une mauvaise configuration des équipements, à des mesures de sécurité inadéquates, à une formation insuffisante et à l'absence de processus de contrôle de la qualité.
Cet article présente des solutions aux problèmes courants liés au travail des métaux, en particulier aux techniques de soudage et de coupage. Nous aborderons les meilleures pratiques pour préparer les matériaux, configurer l'équipement, développer les compétences et garantir la qualité. En abordant les problèmes de manière systématique, les fabricants peuvent minimiser les erreurs de production, maximiser l'efficacité et le rendement, et produire des pièces répondant à des normes strictes.
Préparation du matériel :
La préparation minutieuse des matériaux de base est cruciale pour la réussite des techniques de soudage et de découpage. La saleté, l'huile, la peinture et les oxydes doivent être éliminés de la surface des matériaux pour permettre la fusion et un collage correct. Les contaminants introduisent des incohérences, provoquent des porosités ou des fissures et entravent les performances de l'équipement.
Pour l'acier, le meulage est la méthode de préparation la plus efficace. Il crée une surface fraîche, uniformément rugueuse, optimale pour le soudage. Les meules métalliques ou les disques abrasifs enduits donnent de bons résultats. Lorsque le meulage n'est pas possible, envisagez de poncer avec du papier à grain élevé ou de la laine d'acier.
L'aluminium nécessite un nettoyage particulier. Sa couche d'oxyde natif est beaucoup plus résistante que celle de l'acier et ne s'élimine pas facilement. Les méthodes chimiques sont les plus efficaces. L'immersion des pièces dans une solution d'hydroxyde de sodium ou de potassium à 150-180°F dissout les oxydes en quelques minutes. Commencez toujours par dégraisser l'aluminium à l'aide de solvants tels que l'alcool dénaturé. L'acier inoxydable bénéficie à la fois de traitements mécaniques et chimiques. Perçage et broyage avec une meule en oxyde d'aluminium ou en carbure de silicium prépare aux techniques de soudage et de découpage. Le trempage dans une solution d'acide citrique ou nitrique permet ensuite de décaper la surface et d'éliminer les salissures.
Installation de l'équipement de soudage :
L'installation et la configuration correctes des sources de courant de soudage et des torches ont un impact significatif sur les performances et les résultats du processus. Les opérateurs doivent optimiser la tension, la vitesse du fil et les réglages du débit de gaz en fonction du type et de l'épaisseur du matériau.
Par exemple, le soudage MIG de l'acier utilise généralement une tension de 18 à 25 V et des vitesses de dévidage de 150 à 500 pouces par minute pour des sections fines à épaisses. L'ajout de cellulose ou de gaz de protection au CO2 à raison de 15 à 30 pieds cubes par heure protège la flaque de soudure.
Soudage par impulsion magnétique L'aluminium nécessite une tension encore plus faible (10-15 V) pour un meilleur contrôle du fil. Les mélanges de gaz inertes tels que l'argon et l'hélium permettent une fusion supérieure à celle de l'argon pur. Un débit de gaz supplémentaire, de l'ordre de 1,5 fois les taux standard pour l'acier, élimine mieux l'oxydation. Techniques de soudage et de coupage La position et la géométrie du joint dictent également les réglages de l'équipement. Les soudures verticales vers le haut accumulent facilement les éclaboussures, de sorte que l'abaissement de la tension de 0,5 à 1 V empêche la formation de scories. Les joints d'angle extérieurs sur des tuyaux épais nécessitent une alimentation en fil plus élevée pour un remplissage adéquat du cordon ? Les mécanismes tels que les rouleaux d'entraînement, le revêtement de la torche et l'embout de contact s'usent avec le temps.
Vérifiez régulièrement qu'ils ne sont pas trop serrés, qu'ils ne présentent pas de fissures et qu'ils ne sont pas encrassés, ce qui entraverait l'alimentation en fil. Remplacez les consommables avant que leurs performances ne se dégradent. Tous les câbles alimentant l'équipement de soudage et de coupage doivent être correctement dimensionnés pour éviter toute surchauffe en cas de charge de travail. La sécurité incendie est également essentielle - gardez les espaces propres et secs avec des extincteurs à proximité. En optimisant les réglages des machines, les fabricants produisent des soudures plus solides et de meilleure qualité.
Installation de l'équipement de coupe :
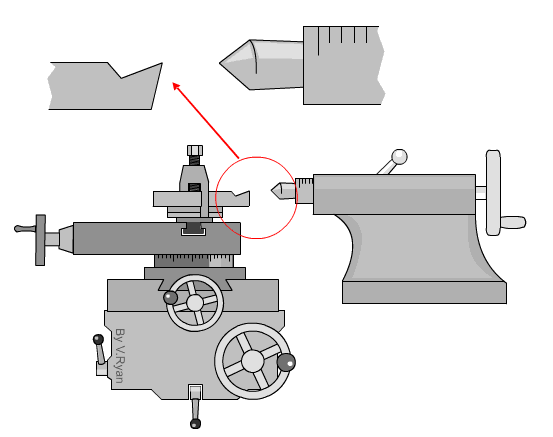
Qu'il s'agisse de plasma, d'oxy-combustible, de laser ou d'eau ET, usinage de pointe Pour obtenir des résultats précis, il faut calibrer et régler la machine avec soin. Pour les torches à plasma, le courant, la pression du gaz et la vitesse de coupe fonctionnent en tandem. Des pressions d'air et de gaz plasma adéquates produisent un arc et une qualité de coupe optimaux à des vitesses de déplacement élevées. Les pressions trop restreintes coupent trop lentement, tandis que les débits excessifs soufflent du métal en fusion et diminuent le contrôle de la coupe.
L'installation de l'oxycombustion se concentre sur le mélange de gaz et les pressions. L'acétylène coupe bien l'acier avec 25-30 psi d'oxygène et 10-15 psi d'acétylène dans le chalumeau. Ajustez les pressions à la hausse ou à la baisse en fonction de l'épaisseur et du matériau à découper pour contrôler la forme de la flamme et les effets de l'oxydation.
Les découpeurs laser doivent aligner des miroirs, focaliser des lentilles et régler la taille du point, la puissance et le gaz d'assistance. Les matériaux en feuilles plus denses nécessitent un point focalisé plus petit, tandis que les plaques plus épaisses sont soudées avec des faisceaux plus grands et moins concentrés.
Découpe au jet d'eau Les systèmes d'aspiration et d'épuration des eaux impliquent le réglage de la taille des buses, de la vitesse d'alimentation en abrasif et de la pression d'eau en fonction de la dureté et de l'épaisseur du matériau et des attributs de qualité de coupe souhaités, tels que la qualité des arêtes en fonction de la vitesse.
Tous les découpeurs ont besoin de réservoirs et de composants de torche propres et bien entretenus, ainsi que de composants de filtration et de régulation de la pression appropriés. La sécurité incendie reste essentielle avec les chalumeaux oxycombustibles, quelle que soit la qualité de l'installation. Avec des machines optimisées, les fabricants effectuent des coupes répétées et productives.
Techniques de soudage :
La maîtrise des techniques de soudage et de coupage garantit des joints solides et sans défaut qui répondent aux exigences des applications. Pour le SMAW techniques de soudage Sur de l'acier fin, maintenez un petit motif de tissage circulaire à une vitesse de 7 à 15 pouces par minute avec une inclinaison de 2 à 5 degrés de l'extrémité de l'électrode. L'ampérage dépend de la taille de l'électrode - les tiges de 1/8″ fonctionnent bien à 80-120A.
Avec le GMAW, tenez la torche à un angle de poussée de 15 degrés et déplacez-vous en suivant un léger schéma de tissage. Des vitesses de déplacement de 80-150ipm permettent d'obtenir de bonnes vitesses d'avance du fil pour la fusion du matériau de remplissage sans éclaboussures excessives. Un déplacement correct du pistolet permet de conserver la forme de la soudure.
Le FCAW est similaire au GMAW, mais le fil fourré dégage plus de fumée. Prenez le temps d'installer un système d'extraction des fumées adéquat, en particulier pour les soudures horizontales. Tenez le pistolet perpendiculairement et effectuez 3 à 5 passes de cordon à une vitesse de 60 à 100ipm.
La machine SAW permet de fabriquer rapidement des supports rigides grâce à l'alimentation synchrone du fil et à la méthode de la danse de l'arc. Réalisez des coutures plates ou verticales à 100-150ipm en utilisant des oscillations de tissage d'une largeur de 1/2-1″. Optimisez la course pour les profils complets. Les techniques à passages multiples augmentent la résistance. Pour les soudures bout à bout, passez un cordon de tissage à la racine, suivi de cordons ajoutant du mastic pour le capuchon de la deuxième passe à chaud. Les joints de recouvrement nécessitent de légers motifs de tissage chevauchant chaque bord de la soudure.
L'ajustement correct du joint et la sélection du métal d'apport permettent d'obtenir des soudures de qualité. Utilisez E6013 pour l'acier au carbone et E71T-1 pour le soudage MIG de l'acier inoxydable. Le rétrécissement se produit, il faut donc meuler les joints légèrement serrés avant les techniques de soudage et de découpage. Laissez refroidir entre les passes pour éviter les fissures et vérifiez la pénétration complète. En ce qui concerne les techniques transversales, entraînez-vous à maintenir une longueur d'accrochage constante et à développer une force d'angle de tige et une vitesse de déplacement stables pour obtenir des soudures lisses et uniformes conformes aux codes et aux exigences de conception.
Techniques de coupe :
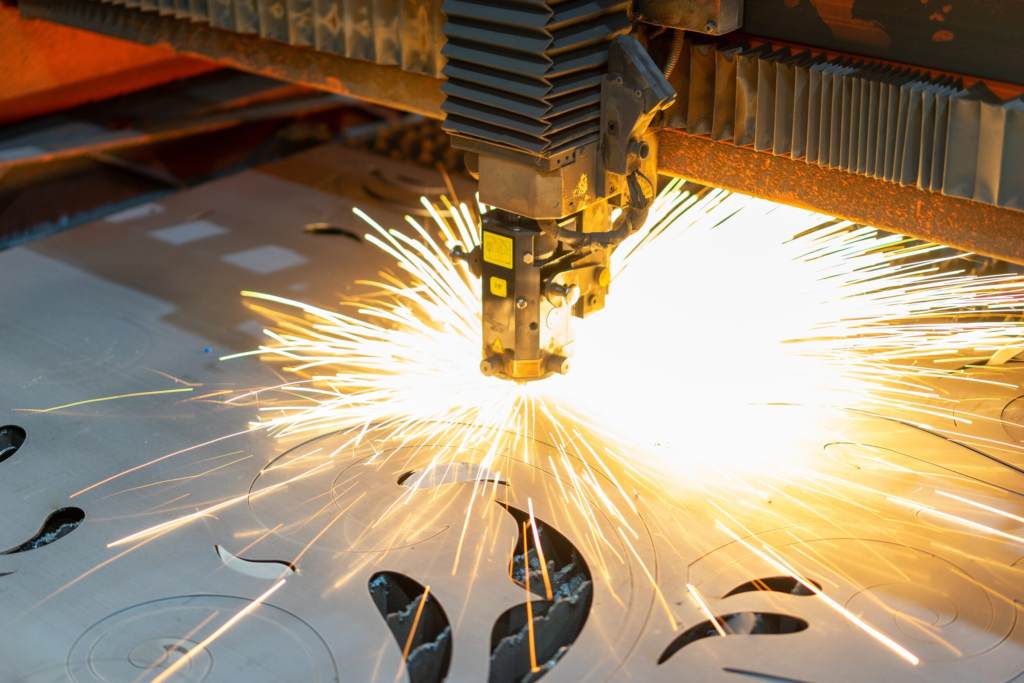
Qu'il s'agisse de découpe droite, circulaire ou de précision, les fabricants de métaux doivent maîtriser les techniques du plasma, de l'oxycombustion, du laser et du système à jet d'eau. Pour la coupe coupes au plasma sur de l'acier doux jusqu'à 1/2″, à une vitesse de 15-25ipm en maintenant un petit trait de scie de 1/8″. Inclinez le chalumeau de 10 à 15 degrés et commencez par le coin supérieur pour obtenir des coupes nettes. Percez les trous de départ à l'aide d'un arc effilé, puis poursuivez avec une coupe droite. Les coupes à l'oxy-combustible sont plus lentes et nécessitent une course uniforme du chalumeau de 3 à 10ipm.
Contrôlez la flamme focalisée de 6-8″ en exerçant une pression régulière sur la roue de coupe. Dirigez la coupe avec la pointe de la flamme neutre pour éviter les retours en arrière. Pour les biseaux, déplacez le chalumeau en même temps que l'angle de la molette de coupe. Découpeuses laser offrent une précision inférieure à une tolérance de 0,005″. Pierce commence par pulser le faisceau en dessous, puis poursuit avec une puissance de coupe continue. Les vitesses de déplacement de 80 à 400ipm dépendent du matériau et de la taille de la buse, mais elles maintiennent une focalisation constante. Les techniques de soudage et de découpe au jet d'eau nécessitent de déplacer le flux dense perpendiculairement à une vitesse de 30-125ipm. Ajustez l'angle de conicité et le débit d'abrasif pour obtenir des performances de coupe en fonction de la dureté. Pour obtenir des pièces régulières, déplacez-vous le long des rayons en douceur plutôt que sur des lignes segmentées.
Le découpage complet renforce la diminution concentrique de la puissance ou de la pression au fur et à mesure que le trou est pénétré. Les torches à plasma coupent les trous dans la largeur de leur trait de scie, tandis que l'oxycoupage peut nécessiter des passages imbriqués de meules de coupe de diamètre croissant, jusqu'à 4″. Des matériaux correctement serrés permettent des mouvements de torche souples et réguliers. Les systèmes à commande numérique répètent les techniques manuelles de manière cohérente sur de nombreuses pièces. Grâce à des conditions de coupe optimisées, les fabricants façonnent avec précision une grande variété de feuilles et de plaques.
Automatisation de la fabrication :
Fabrication l'automatisation introduit des gains de cohérence et de rendement grâce à des processus contrôlés par ordinateur. Les machines CNC à plasma, à laser et à jet d'eau découpent des pièces répétitives à partir de trajectoires programmées presque sans intervention manuelle. Les opérateurs chargent les matériaux sur des tables automatisées qui se déplacent sous les têtes stationnaires.
Les cellules de soudage robotisées exécutent des séquences préprogrammées qui enseignent les techniques de soudage et de découpe aux bras articulés. Les systèmes de vision guident l'adaptation et l'ajustement pour le soudage automatique multipositions sans manipulation supplémentaire des pièces. Les mouvements constants de la torche, les pressions et les vitesses exercées par le robot dépassent les capacités humaines. Les systèmes de palettisation permettent une production non-stop. Les robots chargent et déchargent des palettes de matériaux bruts et finis de Machines CNC sur des tapis roulants menant à plusieurs cellules de travail. Le stockage de l'inventaire à proximité permet d'amortir les lignes.
Les chargeurs de rouleaux automatisés assurent la livraison juste à temps des matériaux aux robots de découpe laser pour une production allégée. Les ravitailleurs de barres approvisionnent de la même manière les centres de tournage et machines à tubes. Le logiciel simplifie l'interfaçage des machines grâce à des langages de programmation et de cinématique communs. Les flux de travail basés sur des modèles génèrent des fichiers de coupe imbriqués et codent les séquences de techniques de soudage et de coupe pour une personnalisation de masse. Les intégrateurs aident à la mise en œuvre et à l'optimisation.
Alors que les coûts d'investissement élevés exigent des volumes importants, l'automatisation offre une précision, une répétabilité et une manipulation de pièces plus grandes ou plus lourdes qui dépassent les capacités manuelles. La production hybride associe l'automatisation à des compétences humaines flexibles pour répondre à des demandes de lignes mixtes. Ensemble, ils augmentent le débit et la qualité pour des opérations de fabrication compétitives.
Conclusion :
Cet article décrit plusieurs domaines clés que les fabricants doivent maîtriser pour produire régulièrement des pièces soudées et coupées de haute qualité avec un minimum de problèmes. La préparation minutieuse des matériaux de base par le nettoyage et tout traitement de surface nécessaire constitue la base. Le réglage correct des techniques de soudage et de découpe, des sources d'énergie et des débits de gaz, ainsi que l'optimisation des paramètres de la machine de découpe au plasma sont également essentiels pour le contrôle du processus et les résultats.
Le développement des compétences manuelles grâce à des techniques telles que le tissage de motifs et le maintien de la vitesse du chalumeau permet de produire des soudures solides et sans défaut, ainsi que des coupes de précision. Compléter le travail manuel par des outils tels que les systèmes automatisés et la robotique permet d'améliorer le rendement, la répétabilité et la sécurité dans les usines. Le respect des meilleures pratiques en matière de manutention, de configuration des équipements et de techniques de soudage et de coupage permet de résoudre de nombreux problèmes courants liés à la fabrication des métaux. Cela permet aux fabricants d'accroître l'efficacité de leurs opérations et de fournir des produits répondant à des normes de qualité rigoureuses, à chaque fois.
FAQs :
Q : Que dois-je rechercher lors de l'achat d'un équipement de fabrication ?
R : Tenez compte de la capacité de la machine, des possibilités d'automatisation, de la garantie et des options de mise à niveau. Recherchez des marques durables et allez voir des unités de démonstration.
Q : La découpe au plasma peut-elle remplacer l'oxy-combustion pour des applications telles que la découpe de tubes ?
R : Le plasma permet des coupes plus rapides et de meilleure qualité, mais ses coûts d'exploitation sont plus élevés. L'oxycombustion reste la meilleure solution pour les matériaux épais et la découpe portable.
Q : Combien coûtent généralement les cellules de soudage robotisées ?
R : Les cellules d'entrée de gamme peuvent commencer à $150K, mais les systèmes à grande échelle peuvent coûter plus de $1M en fonction du nombre de robots, d'outils de soudage et de la protection requise.
Q : Quels sont les EPI requis pour le soudage ?
R : Au minimum, un casque de soudage, des gants, des lunettes de sécurité et des bottes à embout d'acier. Des équipements de protection supplémentaires, tels que des vestes et des écrans, protègent des étincelles et de l'exposition aux UV.
Q : Quelle est l'importance de la préparation du matériau pour le soudage de l'aluminium ?
R : La préparation du matériau est essentielle pour l'aluminium, car sa couche d'oxyde doit être complètement enlevée pour obtenir une bonne adhérence dans la soudure.